By selecting the correct bending direction, refining process control, and applying CNC-based springback compensation, can achieve precise angle profile bending.
Angle profile roll bending is a widely used forming process in construction, machinery, bridges, and decorative structures. This method gradually applies continuous force through roller dies to shape the angle profile into the desired curvature. Compared to stretch bending, roll bending is more efficient, minimizes material waste, and is ideal for large-radius profiles.
During bending, the two legs of the angle profile experience different forces—one undergoes tension while the other is compressed. This uneven stress distribution significantly affects the bending quality. Due to its asymmetrical cross-section, angle profile tends to deform, causing issues such as twisting, section distortion, flange opening, wrinkling, and uneven springback. To ensure precision and stability, special techniques must be applied.
Five Causes of Deformation for Angle Profile Roll Bending
Asymmetrical Structure Leads to Uneven Stress
Angle profile’s two legs experience different deformation levels during bending:
- The outer leg is stretched, increasing the risk of cracking and excessive springback.
- The inner leg is compressed, making it prone to wrinkling or distortion.
- The entire profile may twist, as the different deformation levels create an imbalance in the bending process.
Effect of Bending Direction on Deformation
- Outer bending (legs facing outward) results in a more stable structure but causes greater springback.
- Inner bending (legs facing inward) increases the risk of flange wrinkling and requires additional support.
Offset Neutral Axis Causes Additional Deformation
Since the neutral axis of the angle iron profile is not centrally located, bending generates additional moments. These forces may cause lateral displacement or uneven curvature.
Springback Variation Due to Material Properties
Metal naturally springs back after bending, with the amount of springback depending on material hardness, bending radius, and process settings. Poor control over springback leads to angular errors, preventing the product from meeting design specifications.
Six Methods to Control Deformation
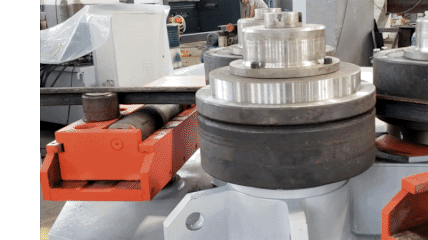
- Method 1#: Using Tooling to Create a Symmetrical Section
Tooling inserts are the most common method for bending aluminum profiles, and they are equally effective for angle profile. By filling the hollow space inside the angle profile with a support structure (such as a mandrel or custom fixture), stress distribution is improved, reducing distortion and flange opening. - Method 2#: Selecting the Optimal Bending Direction
Prefer outer bending to minimize wrinkling in the compressed leg.
For inner bending, apply gradual bending in multiple passes and add extra support to prevent instability. - Method 3#: Designing Proper Roller Dies
Use roller dies that match the specific angle profile dimensions to ensure even force distribution.
Add guiding supports in high-stress areas to prevent lateral displacement. - Method 4#: Optimizing Bending Parameters
Control the feed speed to avoid excessive stress concentration.
Adjust bending pressure to prevent excessive section distortion or inadequate forming.
Apply progressive bending to minimize sudden force application and reduce twisting. - Method 5#: Compensating for Springback
Overbend slightly to compensate for natural springback.
Choose an appropriate bending radius to reduce excessive springback.
Utilize CNC bending systems to monitor angles in real-time and automatically adjust compensation for greater precision. - Method 6#: Adding Lateral Support and Guides
Lateral supports help prevent twisting and lateral deformation.
Proper guide positioning reduces friction-induced deformation and enhances forming accuracy.
Conclusion
Angle profile bending offers high efficiency and material savings, making it a preferred choice in various industries. However, due to its asymmetrical structure, deformation issues like twisting, flange opening, and section distortion are common. Using tooling inserts to create a symmetrical cross-section is the most effective solution. Additionally, optimizing roller die design, adjusting bending parameters, and implementing lateral support significantly reduce deformation.