This guide provides a Tube Bending Radius Chart for hot and roll bending, helping you quickly find the best bending solution to ensure efficiency and quality!
When bending steel tubes, hot bending and roll bending are the most common methods, but each has different radius requirements. Hot bending is ideal for small-radius, thick-walled tubes, while roll bending works best for large-radius, thin-walled tubes.
Common Steel Tube Bending Radius Chart for Hot and Roll Bending
The tube bend radius chart shows the outside diameters of common NPS tubes and the radius to which the tube can be bent using the cold bending process.
NPS | Diameter (mm) | Min. Bending R/Induction Bending (mm) | Min. Bending R/Roll Bending (mm) |
2 | 60.3 | – | ≥700 |
2 1/2 | 73 | – | ≥700 |
3 | 88.9 | ≥135 (≥1.5D) | ≥710 |
3 1/2 | 101.6 | ≥155 (≥1.5D) | ≥810 |
4 | 114.3 | ≥170(≥1.5D) | ≥920 |
5 | 141.3 | ≥220(≥1.5D) | ≥1130 |
6 | 168.3 | ≥250(≥1.5D) | ≥1350 |
8 | 219.1 | ≥350(≥1.5D) | ≥1750 |
10 | 273.0 | ≥700 (≥2.5D) | ≥2200 |
12 | 323.9 | ≥850 (≥2.5D) | ≥2600 |
14 | 355.6 | ≥1100 (≥3.0D) | ≥2850 |
16 | 406.4 | ≥1250(≥3.0D) | ≥3250 |
18 | 457.2 | ≥1400 (≥3.0D) | ≥3660 |
20 | 508.0 | ≥1550(≥3.0D) | ≥4060 |
22 | 558.8 | ≥1700 (≥3.0D) | ≥4470 |
24 | 609.6 | ≥1850(≥3.0D) | ≥4880 |
26 | 660.4 | ≥1980 (≥3.0D) | ≥5280 |
28 | 711.2 | ≥2140 (≥3.0D) | ≥5690 |
30 | 762.0 | ≥2290 (≥3.0D) | ≥6090 |
32 | 812.8 | ≥2450(≥3.0D) | ≥6500 |
34 | 863.6 | ≥2590(≥3.0D) | ≥6900 |
36 | 914.4 | ≥2750(≥3.0D) | ≥7350 |
38 | 965.2 | ≥2900 (≥3.0D) | ≥7750 |
40 | 1016.0 | ≥3050 (≥3.0D) | ≥8150 |
42 | 1066.8 | ≥3200 (≥3.0D) | ≥8550 |
44 | 1117.6 | ≥3350(≥3.0D) | ≥89450 |
46 | 1168.4 | ≥3510 (≥3.0D) | ≥9400 |
48 | 1219.2 | ≥3660(≥3.0D) | ≥9800 |
PDF: https://www.profilebendingmachine.com/wp-content/uploads/2025/03/Tube-Bending-Radius-Chart.pdf
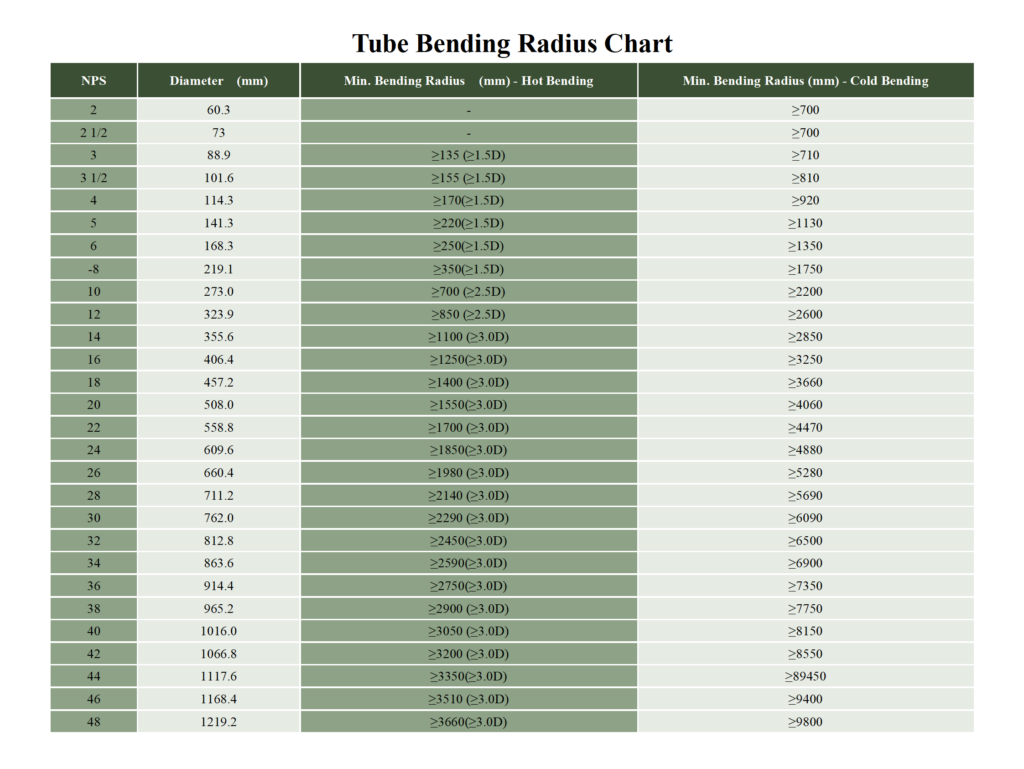
Two Methods of Tube Profile Bending: Induction Bending and Roll Bending
Tube bending can be compared to everyday scenarios to better understand the differences between hot bending (induction bending) and cold bending (roll bending).
Hot Bending (Induction Bending)
Hot bending is like trying to bend a stiff chocolate bar in winter. If you force it, it will snap. But if you warm it with a hairdryer, it softens, making it easier to bend without breaking. Similarly, hot bending uses heat to soften the tube, making it more flexible and easier to shape—especially for large-diameter and thick-walled tubes. This method allows for tight bending radii, sometimes as small as 1.5D. However, it requires specialized heating and bending equipment, which increases costs and energy consumption. Moreover, since heat alters material properties, precise temperature control is essential—just like melting chocolate too much can ruin its texture.
Roll Bending (Profile Bending)
Roll bending is like gently bending a straw by hand. The straw has some flexibility, allowing you to shape it without breaking. However, applying too much force can cause it to flatten or deform. Cold bending follows the same principle—it forms the tube without heating, using a machine to gradually shape it. This method is ideal for aluminum, steel, and stainless steel, especially for large-radius bends that help maintain tube integrity.
Unlike draw bending or press bending, profile bending machines don’t require custom tooling, making them more cost-effective and adaptable to different tube sizes. The process distributes force evenly, ensuring high-quality and durable bends. However, cold bending tends to have more springback, requiring adjustments for precise shapes. Machine accuracy is also critical—otherwise, the bends may be inconsistent.
Simply put, hot bending “softens before shaping,” while cold bending “bends directly with force.”