Tube profile Bending/HSS (Hollow Structural Sections) is a common but challenging task in engineering and construction. Surprisingly, using the “hard way” often results in less deformation, while the “easy way” can cause more noticeable dents.
This article explores HSS bending techniques, parameter selection, and ways to minimize deformation.
Common Tube Profile Bending Techniques
Draw Bending
This method clamps the tube and pulls it around a die to create the desired bend. It’s ideal for thin-walled tubes, stainless steel, and aluminum. The bending radius can be as small as 1D (one tube diameter). It offers high precision and controlled springback, making it perfect for tight-radius bends. You’ll see this used in exhaust pipes, bicycle frames, and furniture manufacturing.
Roll Bending
Here, the tube passes through three rollers with profile bending machines, gradually bending it to a large radius. It works well with steel, aluminum, stainless steel, and HSS tubes. Typical bending radii start at 4D and can go beyond 10D. This method is great for large curves, continuous bends, and minimal material deformation. You’ll find it used in architectural structures, handrails, and piping systems.
Compression Bending
One end of the tube is fixed while the other is pressed against a die, much like a manual pipe bender. It’s commonly used for copper, aluminum, and thin-walled steel tubes with a radius of 3D or more. This is a simple, cost-effective method, best for small-batch production. You’ll see it in HVAC tubing, plumbing, and furniture frames.
Induction Bending
This technique heats a localized section of the tube, softening it for bending. It’s suitable for thick-walled steel, HSS, and large-diameter tubes. The bending radius typically ranges from 1.5D to 5D. Induction bending minimizes material damage and is ideal for large pipes in the oil and gas industry, heavy structures, and aerospace components.
Mandrel Bending
A mandrel is placed inside the tube to prevent thinning or wrinkling during bending. This method is best for thin-walled and high-strength tubes, usually bending at radii between 1.5D and 3D. It ensures the tube maintains its cross-sectional shape, making it essential for high-precision bends. You’ll find it in automotive exhaust systems, medical equipment, and aerospace tubing.
Choosing the Right Parameters
- Tube Diameter (D): Larger diameters need bigger bending radii.
- Wall Thickness (t): Thicker walls resist deformation but require greater bending force.
- Bend Radius (R): Generally, R ≥ 1.5D to avoid cracking or excessive distortion. Further Reading: Tube Bending Radius Chart
- Springback Compensation: Different materials have different springback levels, so adjustments are needed.
When selecting a bending method, consider the tube’s material, thickness, bend radius, and required precision. This ensures optimal bending results while minimizing defects.
Common Rectangular Tube Bending Methods
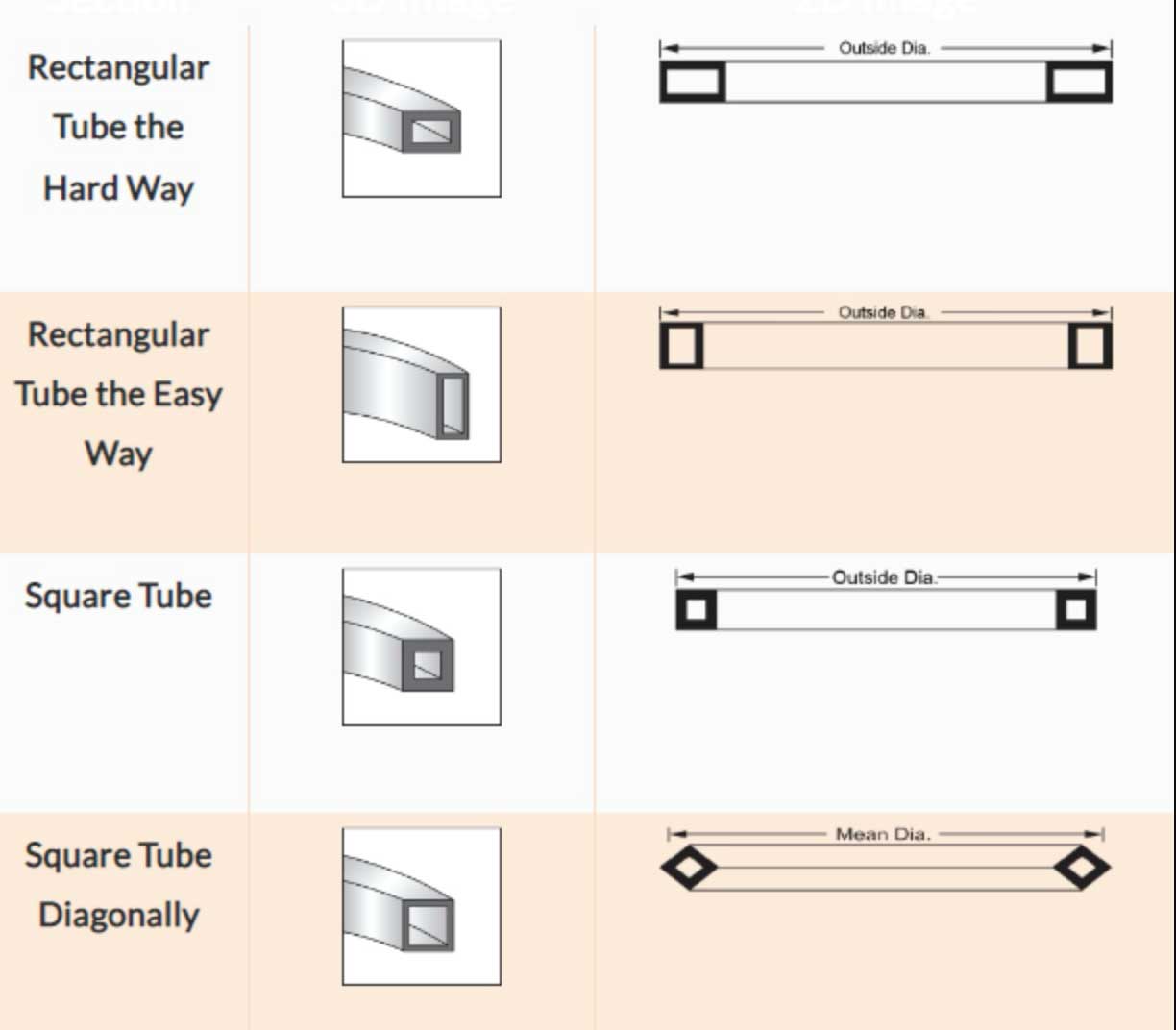
There are three main bending methods for rectangular and square tubes:
- XX-axis bending (Hard Way) – Requires higher force but results in minimal deformation.
- YY-axis bending (Easy Way) – Easier to bend but requires careful control to prevent dents.
- Off-axis rolling – Used when neither the hard nor easy way works, ideal for complex shapes.
Key parameters like CLR (centerline radius), wall thickness (t), and tube size (D) must be considered for optimal bending results.
Hard Way vs. Easy Way Bending
Choosing the right bending method is key to reducing deformation. The hard way means bending along the material’s strong axis, which has a higher moment of inertia—typically the long side of a rectangular tube. Since the strong axis resists bending better, deformation is minimal. The easy way means bending along the weak axis, usually the short side of the tube, which has lower stiffness and tends to deform more.
Factors Affecting Deformation
Several factors influence deformation. First, the greater the difference in cross-section dimensions, the more likely the tube will dent when bent the easy way. For example, a 16″ x 4″ tube is more prone to deformation than an 8″ x 2″ tube. Second, wall thickness plays a major role—thicker walls provide more resistance to bending and reduce deformation. A 0.375″ thick tube will deform less than a 0.250″ thick tube under the same conditions. Finally, bending radius matters—a smaller radius increases deformation, especially for large tubes.
Material Selection & Bending Behavior
Different tube shapes react differently to bending. Round tubes bend more easily and deform less due to their symmetry. For rectangular and square tubes, wall thickness and bending radius are crucial—thicker walls and larger radii reduce deformation. If the bent tube is part of a visible structure, extra care is needed for a clean, precise bend. Additionally, weld seam location and corner radius affect bending consistency, as factory-made rectangular tubes may have hardened edges that increase bending difficulty.
Conclusion
Choosing the right bending method and parameters is essential for reducing deformation in tube profile bending. By considering wall thickness, bending radius, tube dimensions, and bending techniques, you can achieve high precision with minimal distortion. Whether using rotary draw bending, roll bending, incremental bending, or induction bending, understanding each method’s pros and cons helps ensure the best results. Precise bending not only improves functionality but also enhances aesthetics, adding value to engineering and construction projects.
- 👉 Steel Pipe / Tube / HSS Weight Calculator Calculate the exact weight of the tubes before bending.
- 👉 Hollow Circle Pipe Section Modulus Calculator Ensure the pipe meets structural strength requirements.
- 👉 Steel Rectangle Tube Section Modulus Calculator