The cross-section shows the shape of the beam’s profile when you view it perpendicular to its length (e.g., I-beam, U-beam, T-beam, rectangular, or circular cross-sections).
The extrusion process shapes a material (typically metal or plastic) by forcing it through a die to form a continuous profile with a uniform cross-section along its length.
For example, when creating an aluminum beam, manufacturers extrude the material through a die to produce a specific cross-sectional shape (e.g., an I-beam or square tube). This extrusion process ensures the beam retains the same cross-sectional geometry over its entire length, providing consistency and strength for various applications, especially in construction, manufacturing, and structural engineering.
Steel beams
Manufacturers often produce steel beams using methods similar to aluminum, such as extrusion, but adapt the processes to account for steel’s higher strength and unique properties. Steel beams, like aluminum ones, feature a consistent cross-sectional shape along their entire length.
Here are a few common processes used for creating steel beams:
- Hot Rolling: Manufacturers heat steel billets or blooms to high temperatures and pass them through rollers to create cross-sections like I-beams, H-beams, channels, and angles. This method is widely used for structural steel.
- Cold Forming: Manufacturers shape steel at room temperature by bending or folding steel sheets or strips through rollers. This process ensures high precision and smoother surface finishes.
- Extrusion: Manufacturers rarely use extrusion for steel due to its higher strength, which demands much greater force than aluminum.
- Welding: Fabricators weld separate sections, such as plates or smaller parts, to form larger or custom-sized beams like box beams or unique shapes for structural applications.
Steel Beam Types
Steel is ideal for construction due to its high strength-to-weight ratio, durability, and capacity to handle large loads.
- I-beams (H-beams or Universal Beams) are widely used for structural support.
- C-beams and channels provide lighter structural support or framing.
- T-beams, L-beams, and angles suit specific structural needs.
Hot rolling, cold forming, or welding ensures each steel beam maintains the geometry and strength required for its purpose.
Beam Rolling Applications
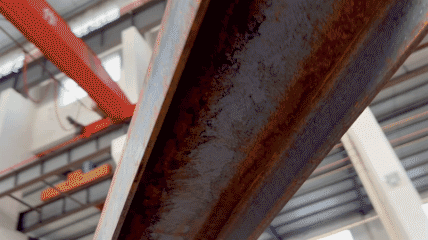
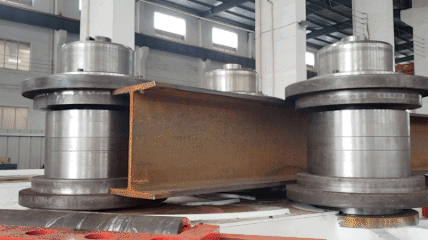
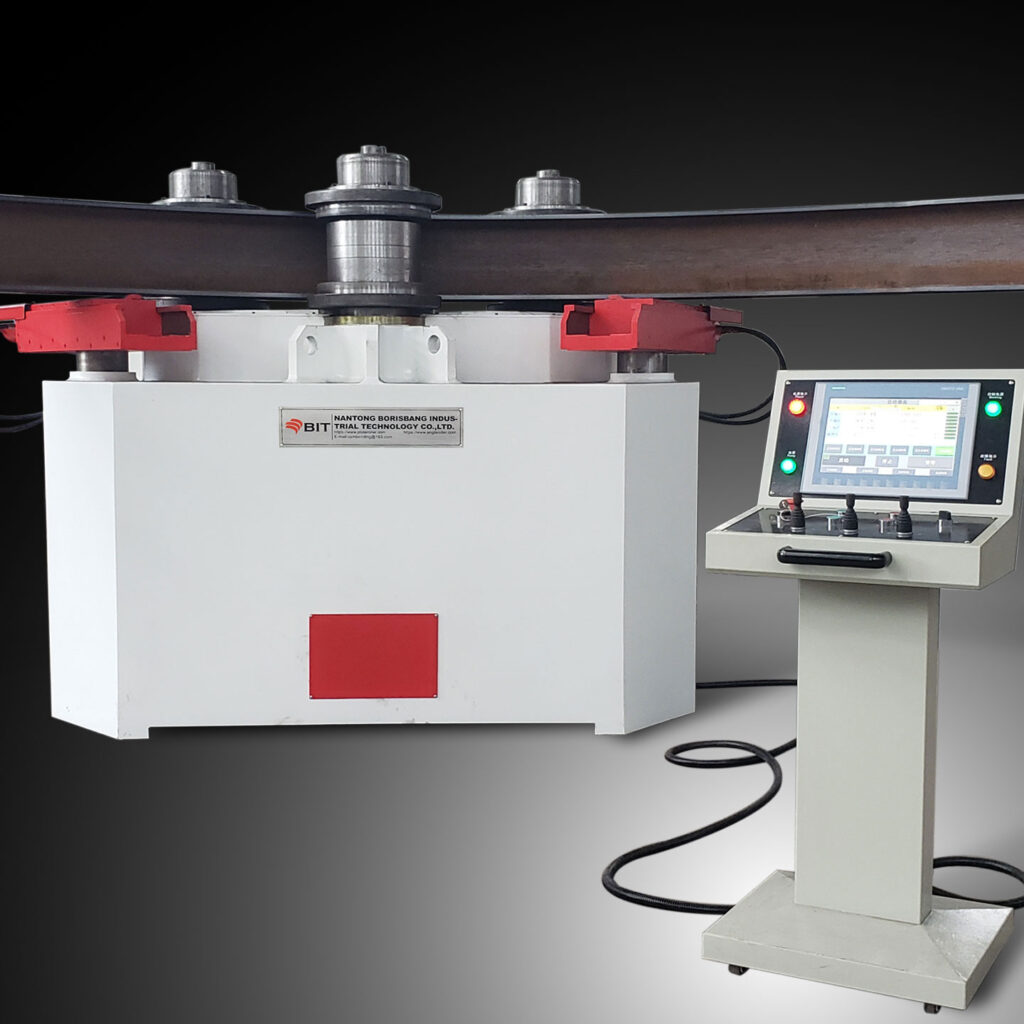
Beam Rolling/Profile bending is essential across multiple industries, contributing to the construction, infrastructure, manufacturing, and architecture sectors. In construction, structural beams provide critical support for buildings, bridges, and towers, ensuring their stability and safety. In infrastructure, curved rails shape railways, and curved beams enhance tunnels, optimizing both structural integrity and functionality. Manufacturing relies on diverse profiles for machines, vehicles, and equipment, enabling the production of custom components. In architecture, designers incorporate custom steel beams into curved roofs, arches, and frames, achieving a perfect balance of aesthetics and functionality in innovative structures.