What we usually call C channel bending includes bending of both steel and aluminum alloy C channels (C-shaped channels). It also relates closely to U-shaped channel steel (U channels).
Channel Profile Bending is a common metalworking process widely used in industries such as construction and machinery manufacturing to create various structural components. Bending C-Channels is a significant part of this process, where C-channel steel is bent to meet specific project requirements. C-channels are typically made from carbon steel, steel, or aluminum. Carbon steel and steel are the most commonly used materials due to their high strength and durability, while aluminum C-channels are used in lightweight applications such as light structures or decorative purposes, though less frequently. The following are the basic knowledge of channel steel:
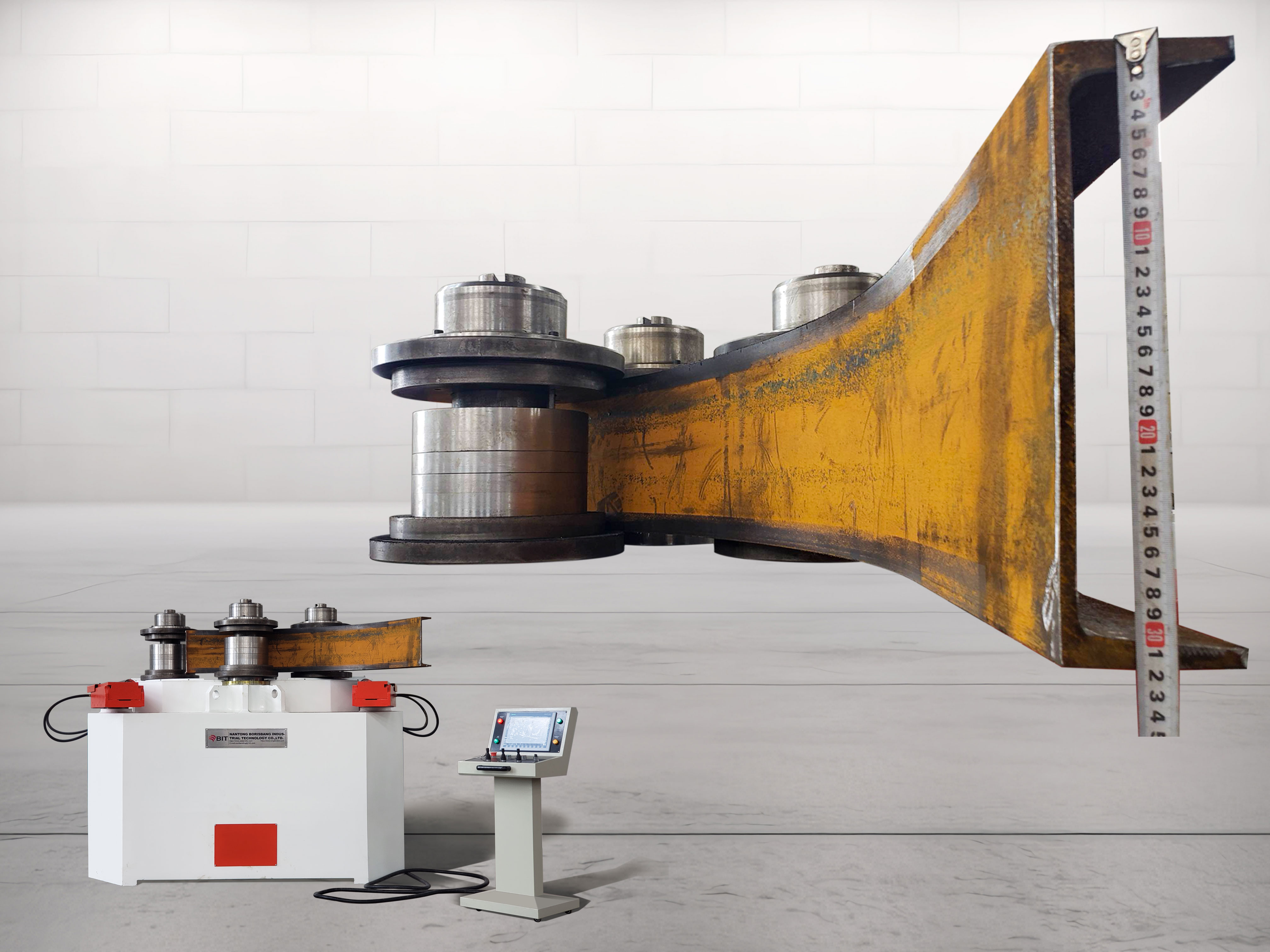
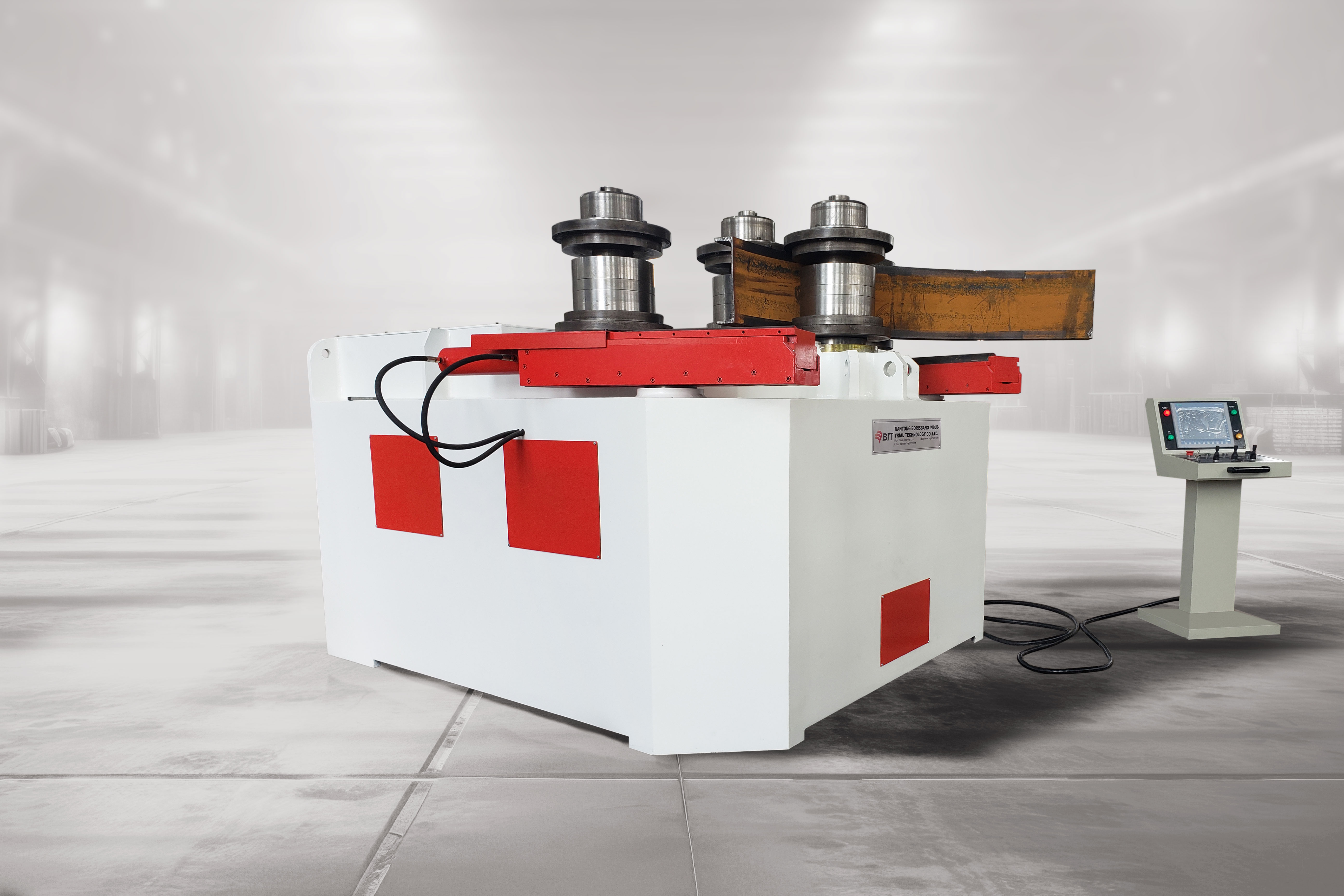
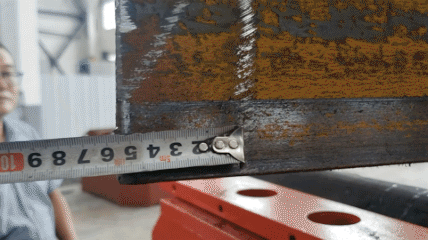
Steel channels come in two main types: structural channels and roll-formed channels (including U-shaped channel steel). Roll-formed channels (U-channel steel made by bending sheet metal) can have varying corner radii, making bending difficult. Precise settings are essential to prevent corner shifting or deformation. Structural channels’ flanges are typically thicker near the web, with reinforced flange-web junctions, featuring square outer corners and rounded inner corners. Roll-formed U-shaped channel steel has a single thickness and lacks the reinforcements of structural channels, resulting in more difficult bending.
Bending Channels
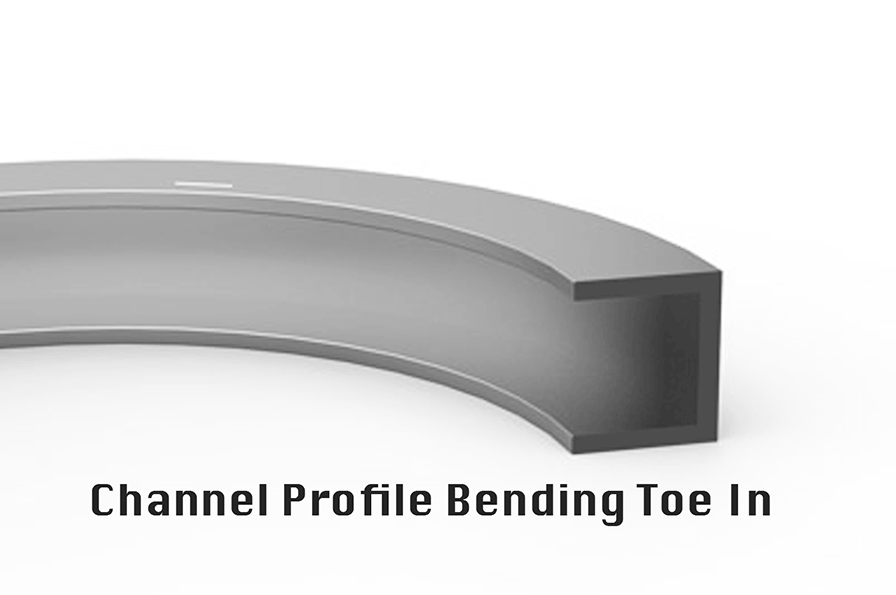
As a common steel material, channel profiles play a vital role in construction, machinery manufacturing, and other industries. While manufacturers produce channel profiles using various materials, carbon steel and steel remain the most prevalent due to their strength and durability. Aluminum channel profiles suit lightweight applications like light structures or decorative purposes, though they are less common.
Bending channel profiles involves curving them into arc-shaped cross-sections. Different processes, such as cold and hot bending, enable channels to form various curves to meet engineering needs. These curved channel profiles serve diverse fields, including construction, machinery, and electrical applications. Engineers often use bent and rolled steel channel profiles for roof trusses, domes, stadiums, canopies, or any structure requiring aesthetic curves.
Cold bending processes ensure a smooth surface with consistent radii along the arc length. The American Institute of Steel Construction (AISC) defines three bending methods: Hard-way (X-X axis bending against the strong axis), Flanges Out, and Flanges In.

- X-X Axis Bending Steel and Aluminum Channel: At room temperature, bending C-channels along the X-X axis (hard way) often causes deformation. The web compresses and, in severe cases, deforms. Flanges bend toward the web center, twisting the section and sometimes creating bulges at the flange-web intersection. Smaller radii or thinner channels increase bending difficulty. Wider webs and flanges add challenges, but tools like web stretchers and mandrels mitigate these issues by preventing web bending or twisting.
- Hot Bending Steel Channel: Hot bending simplifies the process compared to cold bending, achieving smaller radii with less effort. Heating reduces hardness and strength, making the material more pliable. Even heat distribution minimizes residual stress, preventing cracks and uneven deformation. This process supports rapid curvature changes and ensures consistent plastic deformation.
Bending Straight and Curved Unistrut Channels (Including U-shaped Support Channels)
When bending metal profiles such as Unistrut (also known as Flexstrut, Kindorf, Strut, SuperStrut, Metstrut) — common U-shaped support channels — avoid distorting their dimensions. For example, during hard bending, the flanges tend to fold inward.
These straight and curved U-shaped support channels and their fittings are widely used for light structural supports in electrical, mechanical, and HVAC systems.
Standard rolled U-channels (U-shaped channel steel) lack holes for connections, while support channels usually have them. Standard rolled U channels are flat U shapes; support channels have open metal profiles with inward-turned lips.
Formed U-shaped channel steel can be made in sizes and thicknesses not achievable by structural channels, including variations in web width and flange height. Roll-forming such U channels from sheet metal is challenging, making them harder to bend than structural channels.
The P1000 model is usually made from galvanized steel but can also be made from aluminum or stainless steel. Its special cross-section must avoid dents during bending since finished tracks often embed wires or rollers and cannot deform. P1000 uses 12 or 14 gauge steel strips roll-formed into U-shaped C channels with inward flanges. Compared to traditional rolled or extruded parts, formed U channels have weaker deformation resistance and are more prone to instability during roll bending. Therefore, special tooling and individual inspection ensure dimensional and structural integrity.
Most support U-shaped channels are used straight but can also be bent. Like standard rolled U channels, support channels can be bent with flanges inward, outward, or upward — sometimes called “hard” rolled U channels or “web hard” bending. During bending, care must be taken to avoid distorting support channel dimensions, as flanges tend to fold inward under hard bending.
Bending Structural Channels (Including U-shaped Structural Channels)
Among structural steel profiles bent in various ways, bending channels (including U-shaped structural channels) against their strong axis (X-X axis hard way bending) is the most difficult.
Using a three-roll C channel bending machine to bend channels on the X-X axis becomes harder as channels get thinner and their webs and flanges get wider. Cross-sectional deformations often occur. The web is easily compressed, potentially cracking in severe cases. Flanges tend to bend toward the web center, losing the 90-degree angle with the web. Sections can twist, and bulges may appear at web-flange junctions. Smaller bending radii increase difficulty. Attempting to bend the web like hard rebar often causes web deformation. Pressing flanges during bending can push metal inward, especially near the “toe.”
High-quality profile bending machines and experienced operators are essential to successfully bend U-shaped structural channels with small radii.
Bending Aluminum Channels (Including Aluminum U-shaped Channels)
Bending aluminum U-shaped channels is challenging; aluminum channels easily crack under extreme conditions.
Bending aluminum channels into spirals is especially difficult. However, with proper tooling, machines, skilled operators, and controlled processes, impressive bending results can be achieved.
Asymmetric shapes tend to deform or collapse cross-sections, often causing channel failure.
T4 tempering is almost always recommended for bending aluminum channels, though larger radii can use T5 or T6 tempers. The most difficult parts require T4 tempering followed by internal hardening processes. Hardening is done overnight under controlled conditions to eliminate deformation risks.
Bending Methods and Machines
When inspecting “hard-way” bent channels, check flange squareness, web bending, and radius accuracy.
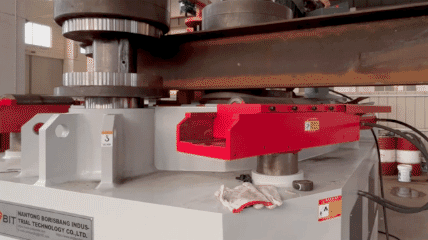
Channel Rolling with Profile Bending Machine
Profile bending machines curve C-channels using three rolls. By adjusting roll gaps, they produce arcs, circles, or other shapes. Due to the channel’s asymmetry, careful support of the inner flange prevents inward tilting. Flanges In or Out rolling achieve smaller radii compared to hard-way rolling.
Roll-Bending Machine for Bending Aluminium U or C Channels
The PBA-1000 profile bending machine offers a max bending capacity of 250mm (Y-Y Axis) or 300mm (X-X Axis). However, for curtain wall materials in T5 condition, we recommend a maximum width of 200mm (X-X Axis) to achieve a minimum bending radius of 1500mm. For widths exceeding 200mm, our PBF series stretch forming machines provide the optimal solution.
Roll-Bending Machine for Steel Channel Bending
With a max bending capacity of 700mm (Y-Y Axis/easy way) and 500mm (X-X Axis/hard way), the standard PBC profile bending machines achieve a minimum bend Ø6000 and Ø40000, respectively. For smaller diameters, stretch forming is recommended, though it comes at a significantly higher cost compared to roll bending.
Channel Bending with Stretch Bending Machine
Stretch bending combines tension and bending to reduce stress and prevent cracks. This method achieves tighter radii and high-quality surface finishes, ideal for applications requiring precision.
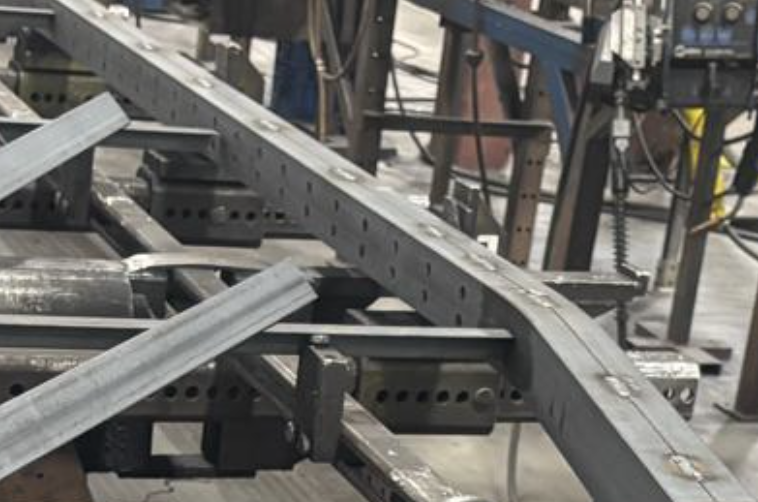
C Channel Bending with Heat Bending
Heat bending machines soften C-channels by heating them, making larger sizes or thicker materials easier to bend. This method prevents cracking or stress-related issues common in cold bending.
Conclusion
Bending C-channels, whether through rolling, stretch bending, or heat bending, offers a versatile approach to creating complex and durable structures. The choice of bending technique depends on factors such as material type, radius requirements, and project specifications.
Recently, a customer inquired about bending two 4 x 4.5 welded C channel tubes along their strong axis. The profile bender manufacturer is evaluating the project with the customer.
Related Links:
- 👉 UPN & American Standard Channel Weight Calculator Find accurate weights before planning your bending operation.
- 👉 C Channel Section Modulus Calculator Check the bending strength and inertia of your C channel.
- 👉 U Channel Bending Machine Discover the right bending machines for U/C channels.