A variable geometry profile bending machine features a three-roll structure but differs from traditional Single Pinch and Double Pinch profile bending machines. It utilizes a design where the side rolls move horizontally while the top roll descends vertically. Compared to a four-roll bending machine, these side rolls provide precise control when bending large, thick-walled profiles. This structure minimizes stress concentration, improves bending accuracy, and ensures consistency.
Note: A wider distance between the side rolls allows for bending larger metal profiles under the same pressure. Meanwhile, the top roll functions like a press brake punch, descending to the required position to form the desired diameter.
Profile Rolling Process
The upper roller can move vertically, and the hydraulic system applies downward pressure to control the bending force. The side rollers can move horizontally, and the force application point can be optimized by adjusting the spacing to achieve adaptability to profiles of different specifications.
Profile Clamping and Positioning
After adjusting the side roll at one end of the machine to the pre-bending position, the profile is fed into the roll gap from the other end, positioned between the top roll and two side rolls. By adjusting the downward pressure of the top roll, the profile is clamped and fixed within the roll gap, ensuring it does not slip, shift, or even fall off during the pre-bending process. Subsequently, the top roll descends, and all three rolls rotate, pre-bending one end of the profile, forming an initial bending arc and leaving the minimum unbent flat area at the profile’s edge.
Roll Bending and Pre-bending the Other End
Once the profile is clamped and one end is pre-bent, the side rolls adjust their positions to ensure that the bending arcs at both ends of the profile are consistent. The three rolls begin to rotate synchronously, driving the profile to move uniformly between the rolls. The top roll continuously applies pressure, gradually forming the desired arc. When the profile reaches the other end, the side rolls adjust again to complete the pre-bending at the other end, ensuring consistent bending at both ends.
Multiple Bending Stages and Profile Extraction
For profiles requiring complex bending, the operator can use the CNC control system to repeatedly adjust the downward pressure of the top roll and the spacing of the side rolls, gradually completing the full-length bending of the profile. Once the profile reaches the preset bending shape, the top roll and side rolls stop moving, and the operator extracts the bent profile from the roll gap, completing the entire process.
Key Points
- The CNC system precisely controls the roll speeds and downward pressure, ensuring the profile bends according to the preset trajectory.
- By adjusting the downward pressure and position of the top roll, the force application point can be brought closer to the bending area of the profile, reducing unnecessary material deformation and improving bending precision.
- All three rolls are main driving rolls, synchronized via the CNC control system. This ensures the profile moves uniformly between the rolls, avoiding material slipping or deformation due to speed differences.
Comparison of Profile Bending Machines
Besides variable geometry bending machines, other common types include Pyramid Bending, Single Pinch, and Double Pinch profile bending machines. Each has distinct advantages and is suited for different applications.
Pyramid Profile Bending Machines
Pyramid profile bending machines, also known as angle roller, are small, vertically oriented machines. Their three rolls are arranged in a pyramid shape: two fixed side rolls at the bottom and a movable top roll. The top roll applies downward pressure to form the bend gradually. The bottom rolls provide rotational force, while the top roll acts as an idler.
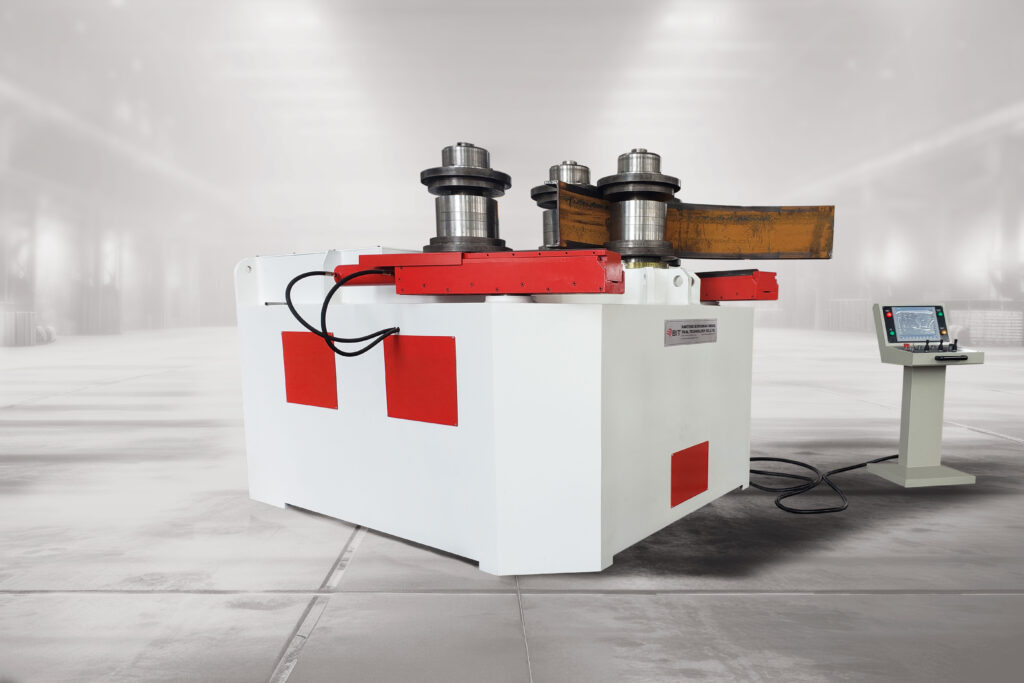
These machines are simple in design, low in maintenance costs, and suitable for small profiles. However, their fixed side rolls limit pre-bending capability, requiring material ends to be cut off, resulting in waste. They also need longer feed strokes, increasing processing time. They are not ideal for small-radius bends or applications demanding high precision.
Single Pinch Profile Bending Machines
A single pinch profile bending machine has one movable side roll, while the other side roll and top roll remain fixed. Operators must manually flip the profile to pre-bend both ends.
This machine is simple in structure, easy to operate, and cost-effective. It is suitable for small workpieces, thin-walled profiles, and standard bending applications. However, it requires additional handling to achieve pre-bending, increasing complexity. It also lacks the precision and capacity needed for large, high-strength profiles and leads to material waste.
Double Pinch Profile Bending Machines
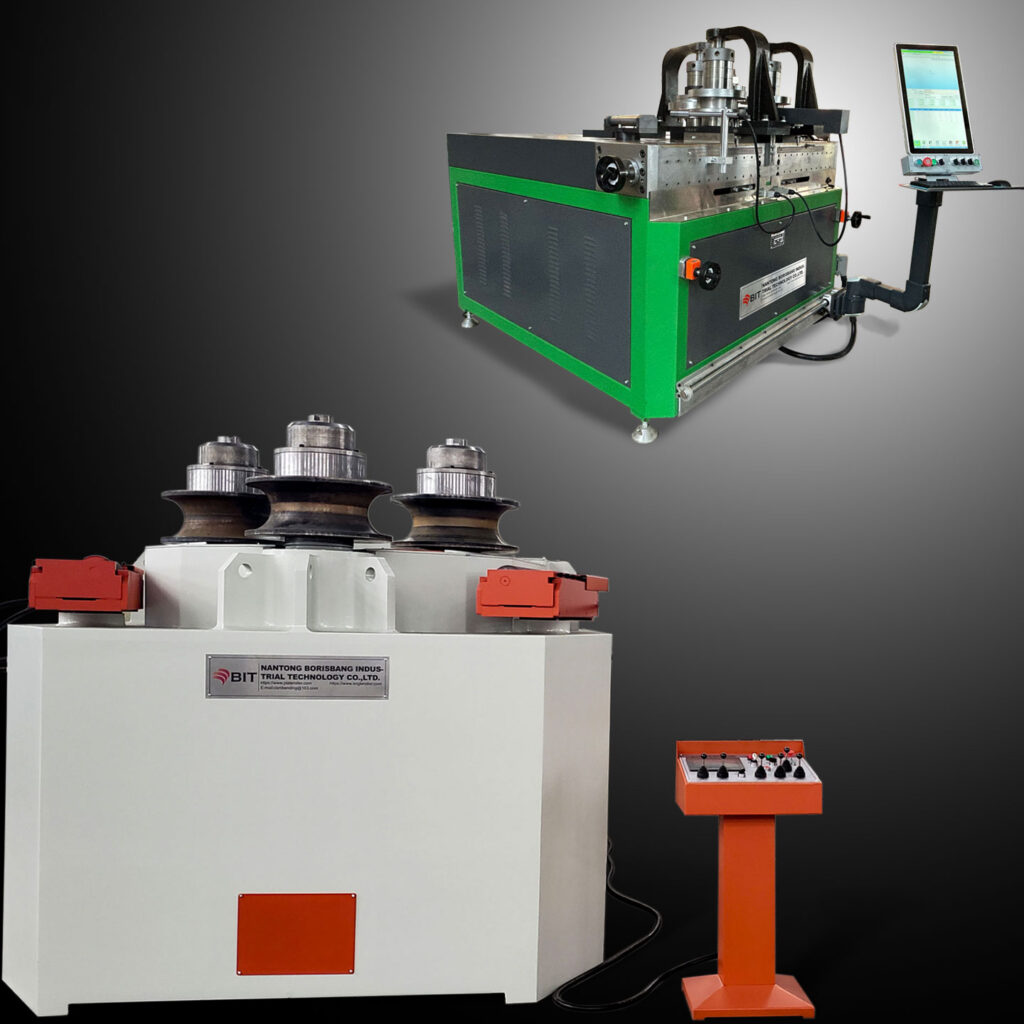
A double pinch machine features two movable side rolls, enabling direct pre-bending without flipping the profile. This improves stability and precision during bending.
With both sides capable of pre-bending, efficiency is higher, and material waste is reduced. These machines offer excellent accuracy and are suitable for high-precision applications. However, they have limitations when handling ultra-large or thick-walled profiles. Additionally, they are more expensive than single pinch machines.
Variable Geometry Profile Bending Machines
Unlike other types, variable geometry bending machines use a unique design where the side rolls move horizontally, and the top roll descends. This allows operators to adjust roll spacing to optimize the bending process for different profiles.
They are particularly suited for large, thick-walled profiles due to their superior bending force. Their adjustable structure distributes force more effectively, minimizing springback and improving accuracy. While offering flexibility for various profile sizes, these machines are complex and costlier than other types.
Conclusion
For industries dealing with large steel structures, shipbuilding frames, long-span bridges, and aerospace components, a variable geometry profile bending machine is the best choice. For standard profiles, window frames, and common construction applications, Double Pinch or Single Pinch machines are more suitable. Pyramid bending machines are ideal for small workshops where precision requirements are low.