The flange rolling machines for PBC are the best solution designed to roll bending flat bar and angle iron into precision flanges. Whether you’re producing flat flanges for ductwork(even Heavy-Duty wind power, gear manufacturing) or angle ring flanges for industrial piping, PBC delivers reliable performance and consistent quality.
Full Set of Combination Dies for Immediate Use
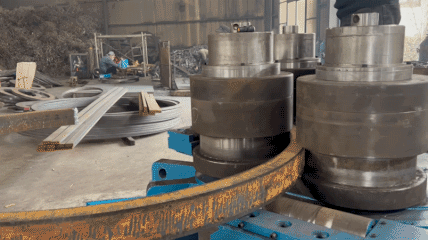
Unlike other flange bending machines that require separate tool purchases, PBC comes equipped with a full set of combination dies, ready to handle both flat bar and angle steel flanges out of the box. This built-in tooling package saves cost, reduces downtime, and makes setup faster for every job.
In addition, PBC provides superior bending capacity compared to similar-class machines. With higher torque and reinforced frame design, it effortlessly handles large-section profiles and heavy materials, offering the strength and flexibility required for challenging flange projects.
PBC’s design ensures precise X-X axis roll bending for flat bar flanges and integrates an Anti-Twist Correction System to solve common issues during leg-in angle flange bending.
Flange Rolling for Heavy-Duty Applications
Flange rolling is used for producing heavy-duty flanges, which have wide applications in industries ranging from offshore wind power to gear manufacturing and pipeline engineering. Rolling such large flanges requires specialized equipment, such as giant profile bending machines capable of producing non-standard size flanges, including those with thicknesses up to 340mm and very large diameters.
Customized Solutions for Heavy Flanges
For rolling heavy-duty flanges, such as the standard PBC-700 model that handles flanges with thicknesses up to 240mm, we can also customize machines that handle flanges with thicknesses exceeding 300mm according to customer needs. These profile bending machines need to have a more compact geometric structure, equipped with extended card clamps to reduce roll shaft deformation, and special roll shafts designed for heavy-duty applications to ensure both forming accuracy and equipment longevity.
Explore more about PBC Angle Roller for heavy-duty flange production and see how it supports various bar and flange forming techniques in our detailed guide on bar bending.
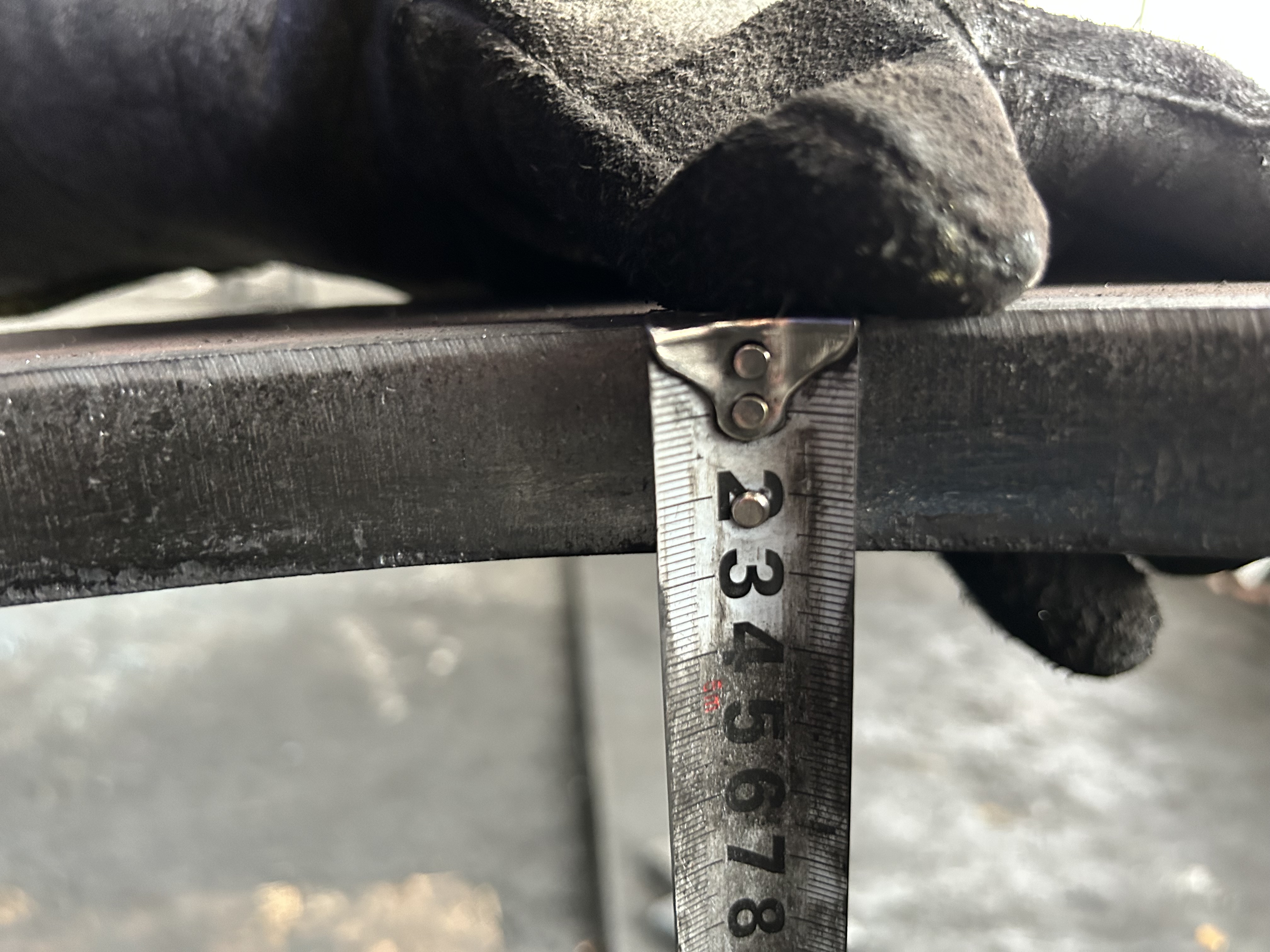
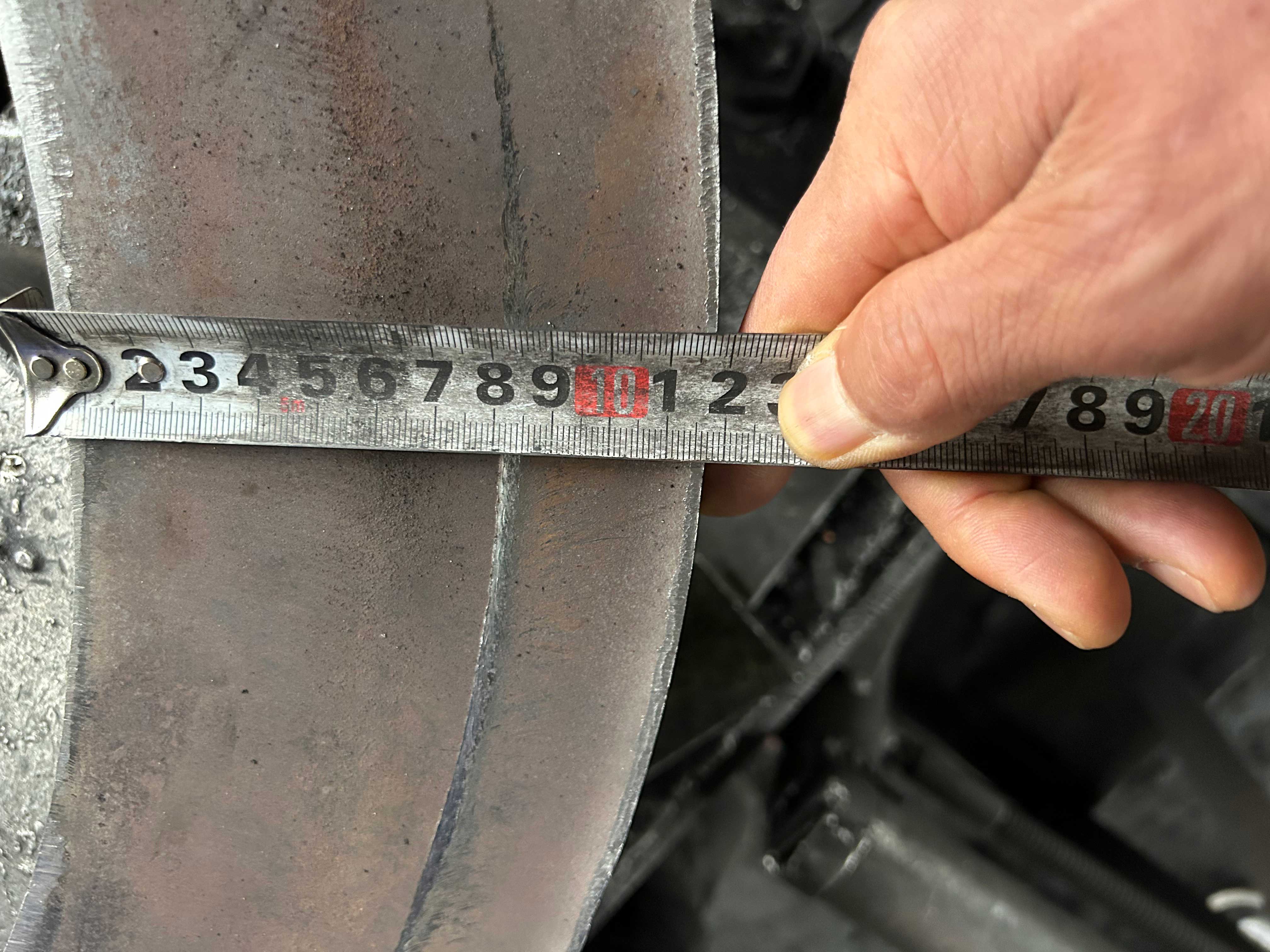
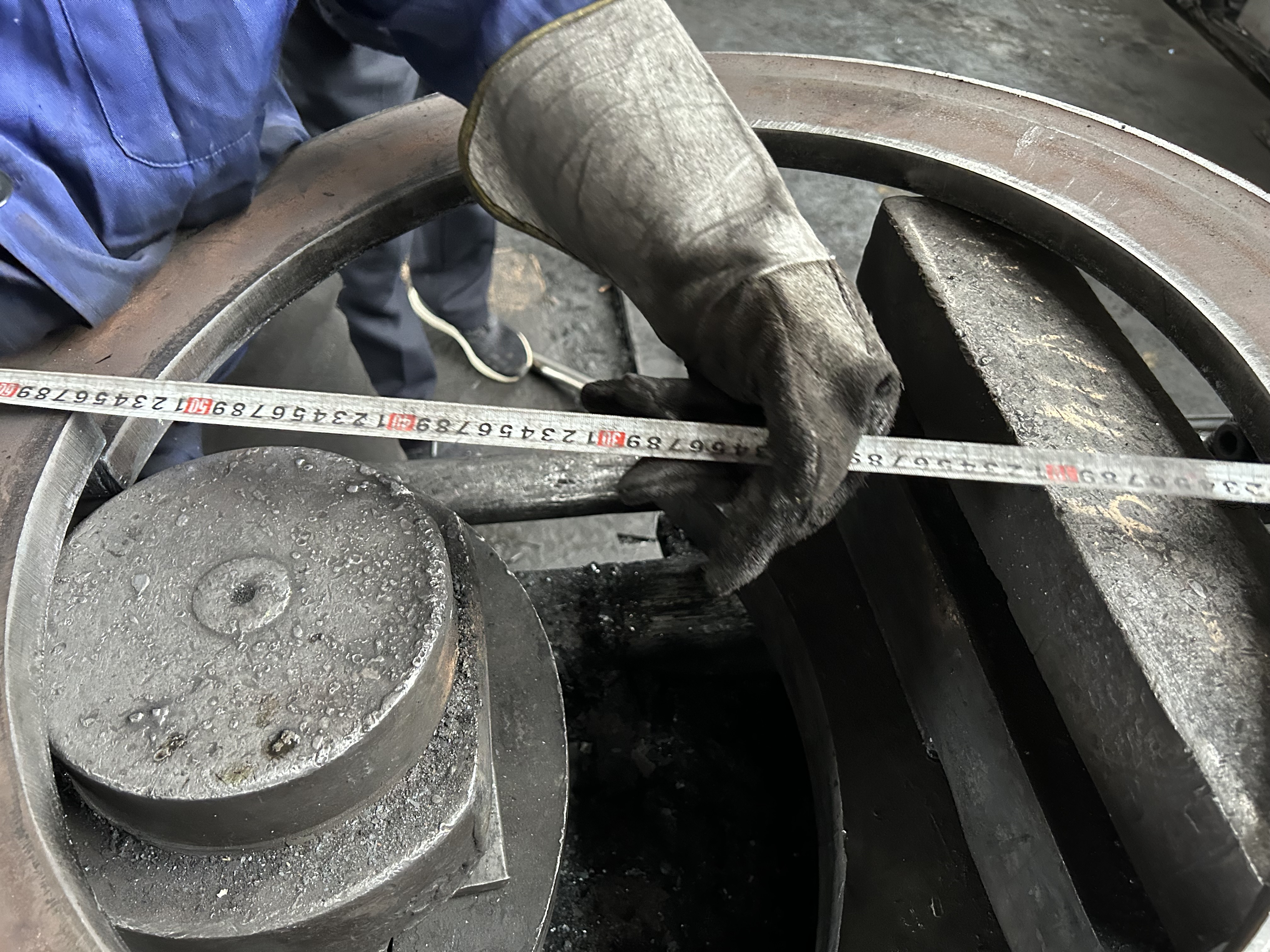
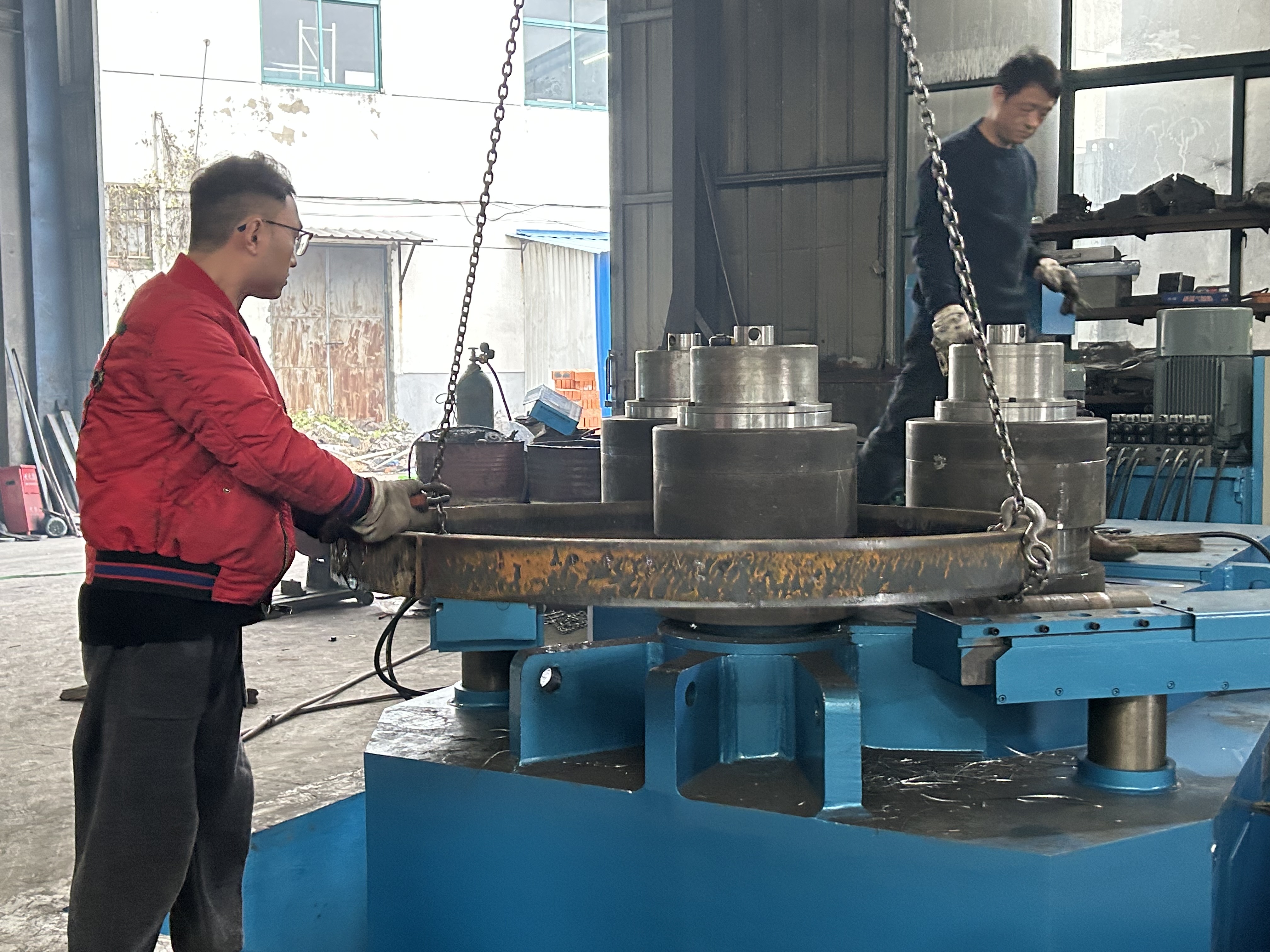
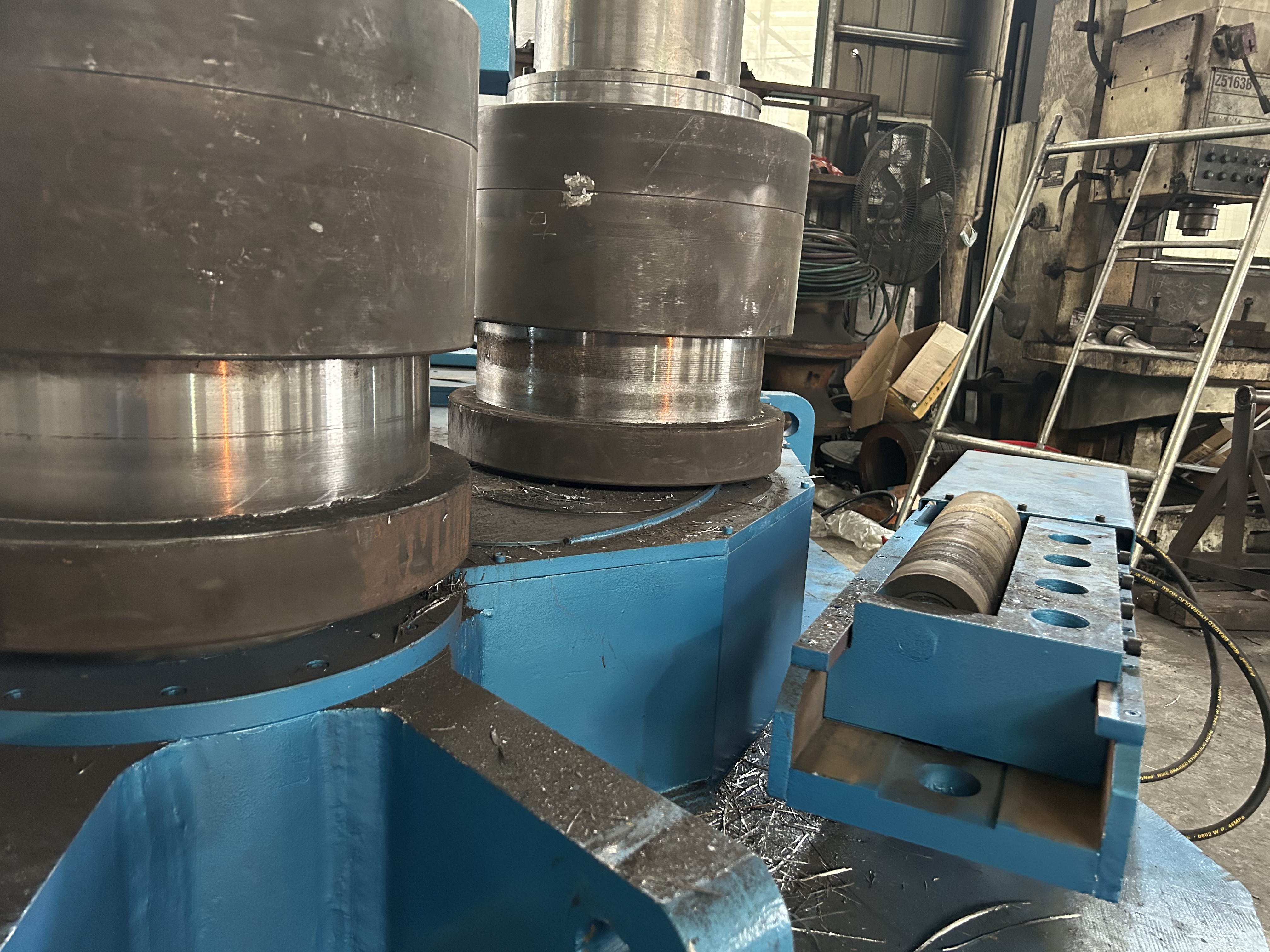
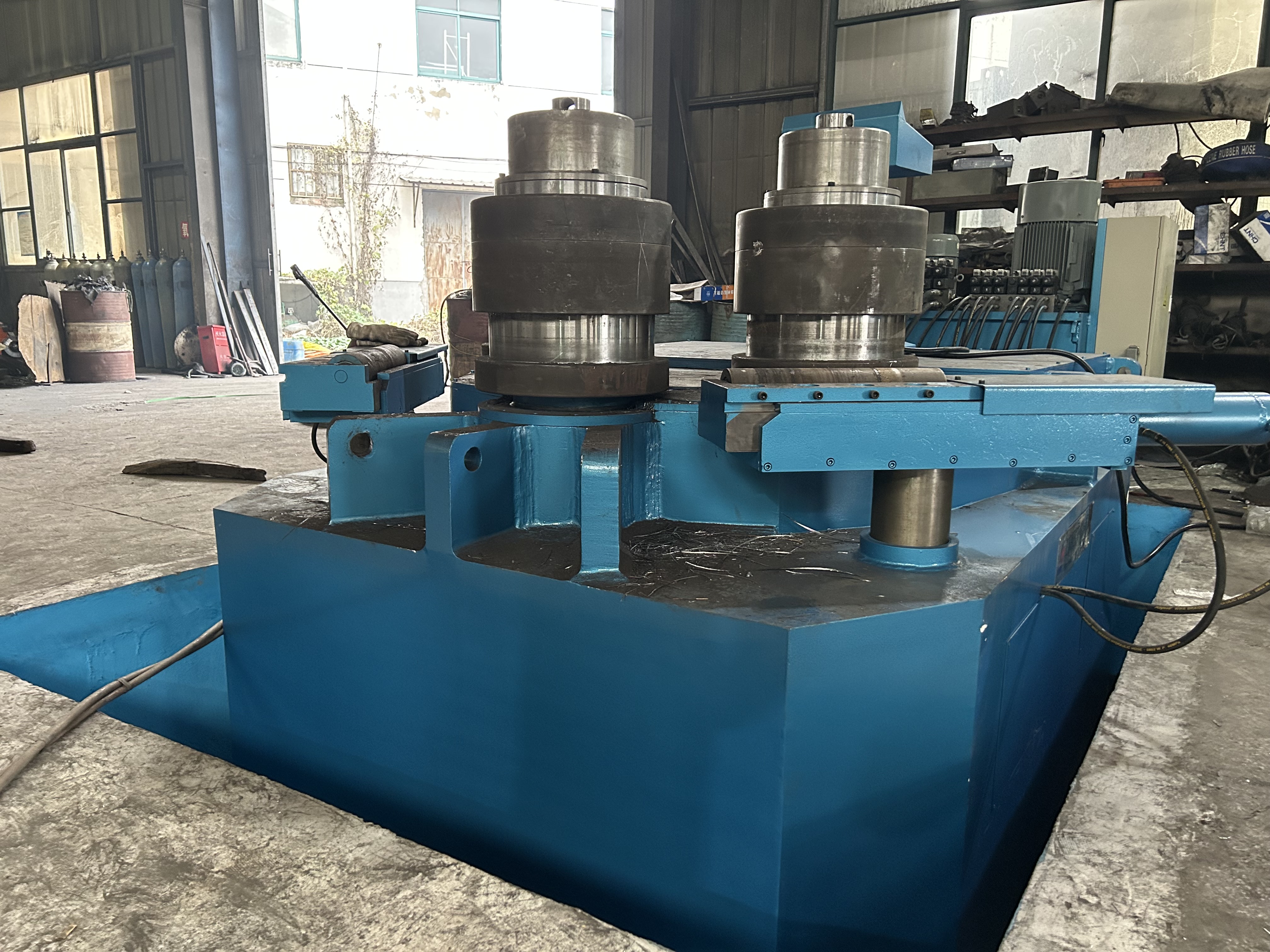
With its powerful specs, built-in tooling, and profile versatility, PBC stands out as a top-tier flange rolling machine for industrial applications.
Free Flat Bar Bending Calculator
To further support your bending operations, we also provide a free Flat Bar Bending Calculator to help estimate bending force, radius, and material requirements. This tool is ideal for engineers and fabricators who need fast, accurate calculations before production. Whether you’re working with mild steel, aluminum, or stainless flat bars, it simplifies planning and ensures you get the most out of your flange bending machine.
Basic Parameters of 3 Popular PBC Flange Bending Machines
Item | PBC 200 | PBC 300 | PBC 360 |
---|---|---|---|
Section Modulus (cm³) | 45-75 | 75-240 | 180-32 |
Bending Speed (m/min) | 4.5 | 4.5 | 4.5 |
Guide Rolls Moving Speed (m/min) | 1.6 | 1.6 | 1.6 |
Upper Shaft Diameter (mm) | 140 | 180 | 220 |
Lower Shaft Diameter (mm) | 130 | 160 | 180 |
Bending Roller Diameter (mm) | 385 | 460 | 520 |
Hydraulic Motor Power (kW) | 11.0 | 11.0 | 15.0 |
Weight (kg) | 4500 | 3600 | 5000 |
Diameter (mm) | 1600×1600×1350 | 2500×2530×1700 | 3200×2600×1800 |
![]() | ![]() | ![]() |
Capacity Table for Bent Profiles
Profile & Bending Method | PBC-200 | PBC-300 | PBC-360 | Mold & Tool |
---|---|---|---|---|
![]() | 120×25 Φ1000 | 150×30 Φ1500 | 175×40 Φ2500 | ○ |
![]() | 250×30 Φ1000 | 250×40 Φ1000 | 350×40 Φ1500 | ○● |
![]() | 70×70 Φ700 | 80×80 Φ1500 | 110×110 Φ1600 | ○ |
![]() | Φ80 Φ800 | Φ100 Φ1000 | Ø 125 Φ1200 | ● |
![]() | Φ142 Φ1800 | Φ170 Φ2000 | Φ190 Φ2500 | ● |
![]() | 100×100×6.5 Φ1500 | 120x120x8 Φ3000 | 150×150×8 Φ5000 | ○● |
![]() | H: max.60 W: max.120 Φ1500 | H: max.70 W: max.130 Φ3000 | H: max.80 W: max.160 Φ5000 | ○● |
![]() | H: max.120 W: max.60 Φ1500 | H: max.140 W: max.100 Φ2000 | H: max.160 W: max.120 Φ2500 | ○● |
![]() | 100×100×12 Φ1250 | 130x130x15 Φ1200 | 160×160×20 Φ1800 | ○△ |
![]() | 120×120×12 Φ1250 | 150x150x16 Φ1000 | 160×160×20 Φ3000 mm | ○△ |
![]() | 100×100×12 Φ1500 | 130x130x15 Φ1700 | 150x150x20 Φ2000 | ○△ |
![]() | 120×120×13 Φ1250 | 150x150x15 Φ1200 | 160x160x20 Φ1400 | ○△ |
![]() | 140×140×15 Φ1250 | 150x150x15 Φ1300 | 160x160x20 Φ1500 | ○△ |
![]() | UPN 200 Φ1000 | UPN 300×100 Φ1100 | UPN 360 Φ1400 | ○● |
![]() | UPN 200 Φ900 | UPN 300×100 Φ1100 | UPN 360 Φ1200 | ○● |
![]() | UPN 100×50 Φ8000 | UPN 160×65 Φ9000 | UPN 200×75 Φ11000 | ○●▲ |
![]() | IPE 200 HEA 140 HEB 120 Φ900 | IPE 300 HEA 180 HEB 160 Ø 1100 – | IPE 360 HEA 240 HEB 200 Ø 1500 | ○● |
![]() | PE 120 Φ2500 HEA Max. Section Mudulus: 45-75 cm³ | IPE 160 Φ3400 HEA 140 Φ6000 | IPE 200 Φ5000 HEA 180 Φ4500 | ○●▲ |
○: Standard Roller
●: Custom Roller
△:Standard Tool
▲: Custom Tool
○●: Standard Roller or Custom Roller