As the profile passes through the rollers, continuous pressure causes it to bend permanently without cracking.
Profile rolling/roll-bending(also called section bending) is a widely used metal forming process capable of bending various alloy profiles – including aluminum, steel (angle profile, channel profile, flat bar profile, etc.), copper, and titanium – into arcs or complex shapes without compromising the material’s structural integrity.
What is Profile Roll-Bending Process?
Profile roll-bending is one of the core metal section forming techniques, alongside stretch forming. It offers exceptional flexibility, enabling metal sheets or aluminum extrusions to be shaped into arcs, circles, and other complex curves. By applying force through rollers, the profile gradually bends to the desired radius with high precision.
The profile bending process relies on the principle of plastic deformation—continuous pressure as the profile passes through the rollers causes it to bend permanently without cracking. The resulting curvature depends on several factors: roller diameter, material thickness and composition, pressure application, and feeding speed.
A key advantage of profile roll-bending is its ability to form smooth, uniform curves in heavy structural profiles. It’s ideal for architectural supports and mechanical components with complex geometries—shapes that are difficult or impossible to achieve with press brakes. Combining precision and productivity, profile rolling efficiently transforms raw materials into functional parts.
Notes: The rollers are configured according to the shape of the profile to prevent cross-sectional deformation during the bending process. By changing the relative position of the rollers along the Y-axis, a bending profile with continuously varying radii can be formed.
Through control of the Z-axis, the profile can be bent into three dimensions, and even customized torsion bending devices can be added for off-axis bending.
Material Selection for Metal Profiles
Nearly all metallic materials can be processed using profile bending machines, but the actual forming results vary significantly depending on material properties.
- Steel profiles exhibit notable elastic recovery (springback) due to their material elasticity;
- Aluminum alloys offer better formability but are more sensitive to temperature variations;
- Copper materials demonstrate excellent ductility but are prone to work hardening;
- Titanium alloys present greater forming challenges due to their high strength.
Critical Quality Factors
Cross-sectional dimensional accuracy: Even minor dimensional variations (as small as fractions of a millimeter) or uneven bending resistance can lead to irregular arc diameters in the final product.
Straightening requirements: Any initial deformation may cause localized over-bending or under-bending. Precise control of straightening pressure is crucial, as improper pressure (either excessive or insufficient) will create uneven internal stress distribution, ultimately affecting rolling precision.
Surface pretreatment: Strict cleaning standards require oil residue below 5μm and derusting to Sa2.5 grade.
To ensure processing quality, workpieces must meet three fundamental requirements: clean and contamination-free surfaces, precise cross-sectional dimensions, and straight initial condition. Process adaptation requires pre-calculation of theoretical bending radius (including springback compensation), proper feed rate gradient setting, and planning of intermediate recovery time for multi-pass bending.
Preparation Processes Before Profile Roll-Bending
For common flanged profiles like angle steel and T-beams, chamfering represents the most critical preparatory step:
Material feeding and discharging: Chamfered edges prevent interference between sharp profile corners and rollers, facilitating both machine insertion and post-straightening/bending removal;
Equipment and workpiece protection: Reduces roller wear from sharp edges while minimizing stress concentration at flange areas during bending, preventing material deformation or cracking;
Quality enhancement: Chamfering ensures more uniform stress distribution during bending, yielding smoother curves and higher dimensional accuracy.
Example of profile prepared with chamfer
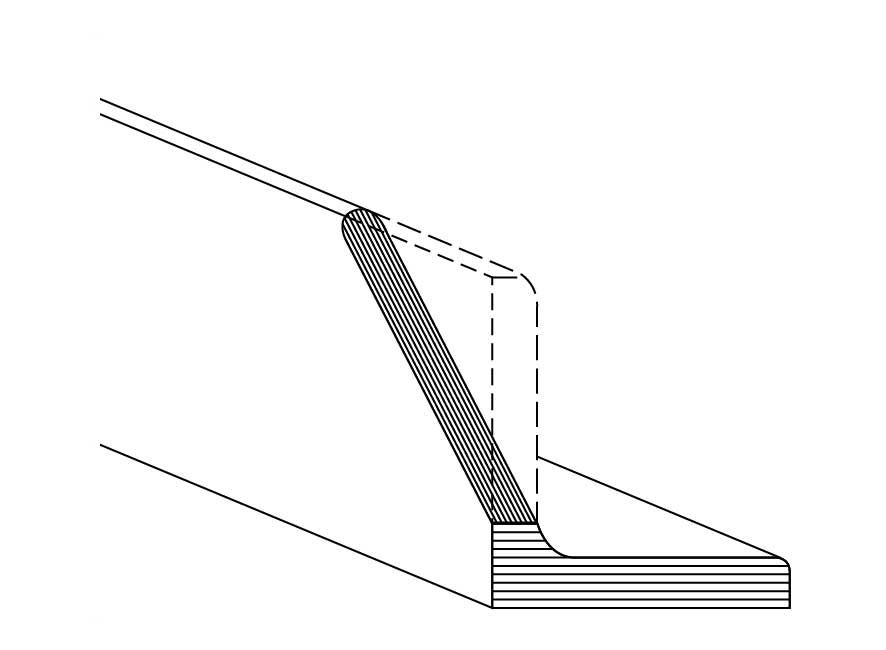
Chamfered angle iron section prepared for bending with outside flange
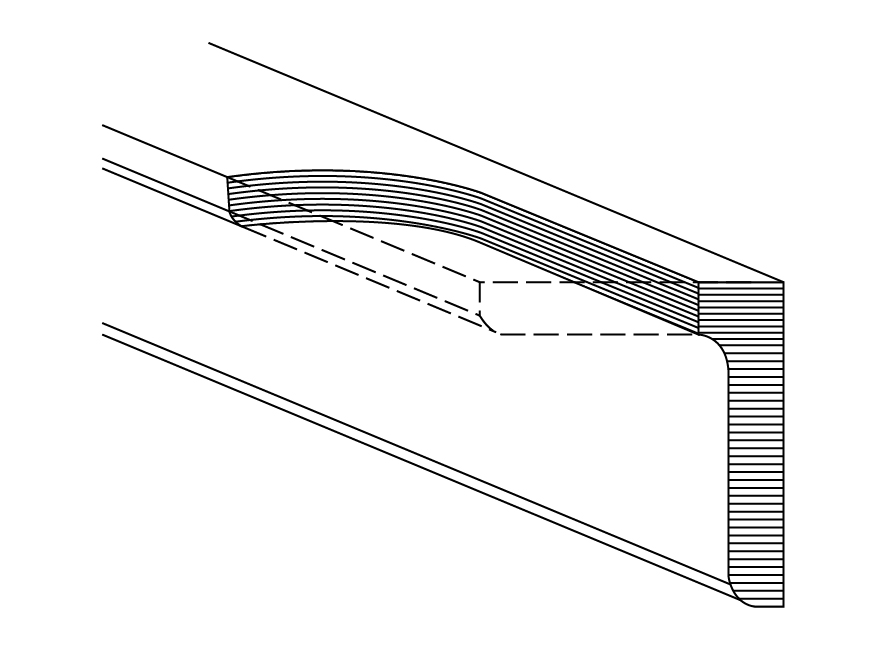
Chamfered angle iron section for bending with internal flange
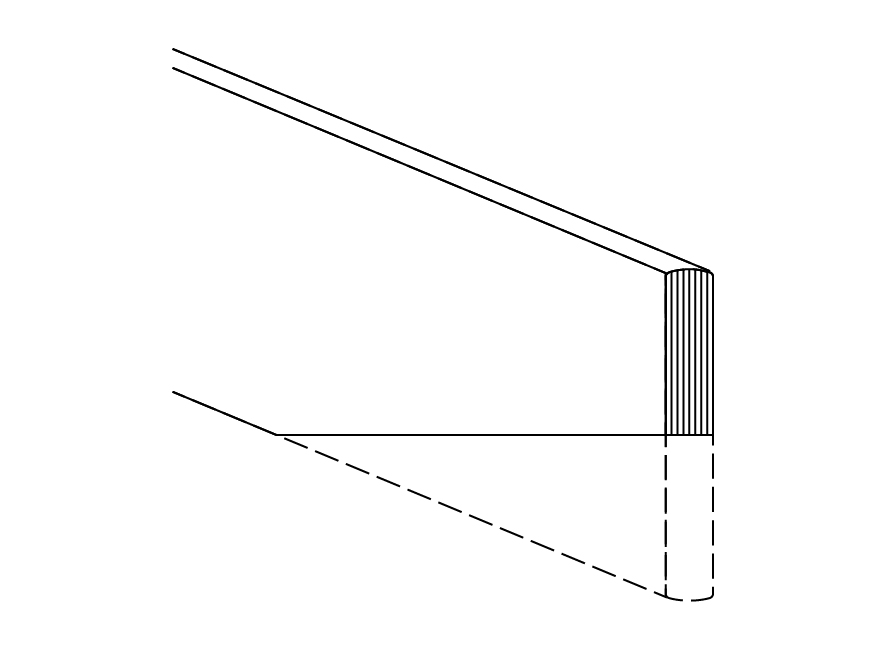
Chamfered Flat bar section prepared for edgewise bending
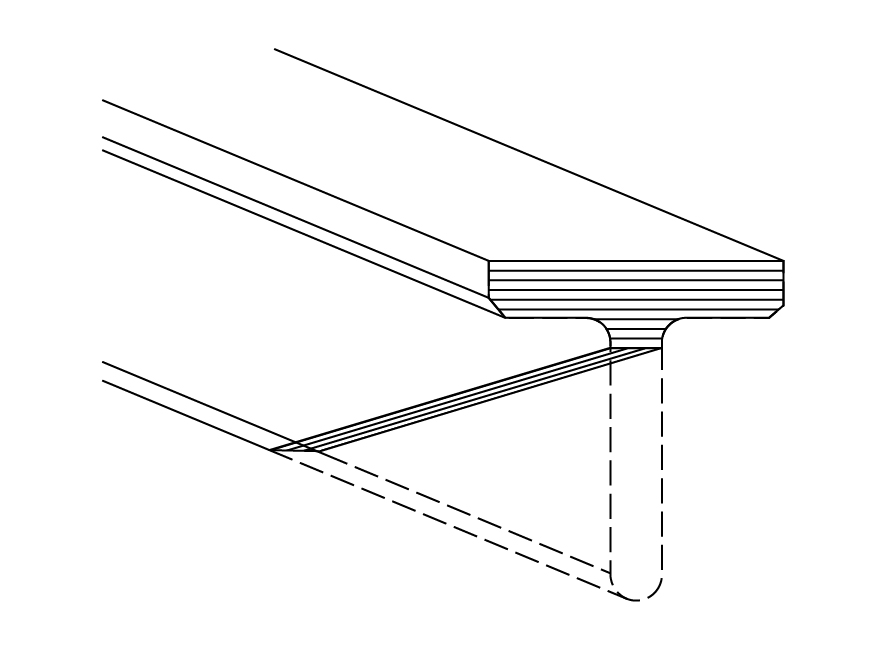
Chamfered T section for profile roll-bending
Bending Roll Configuration
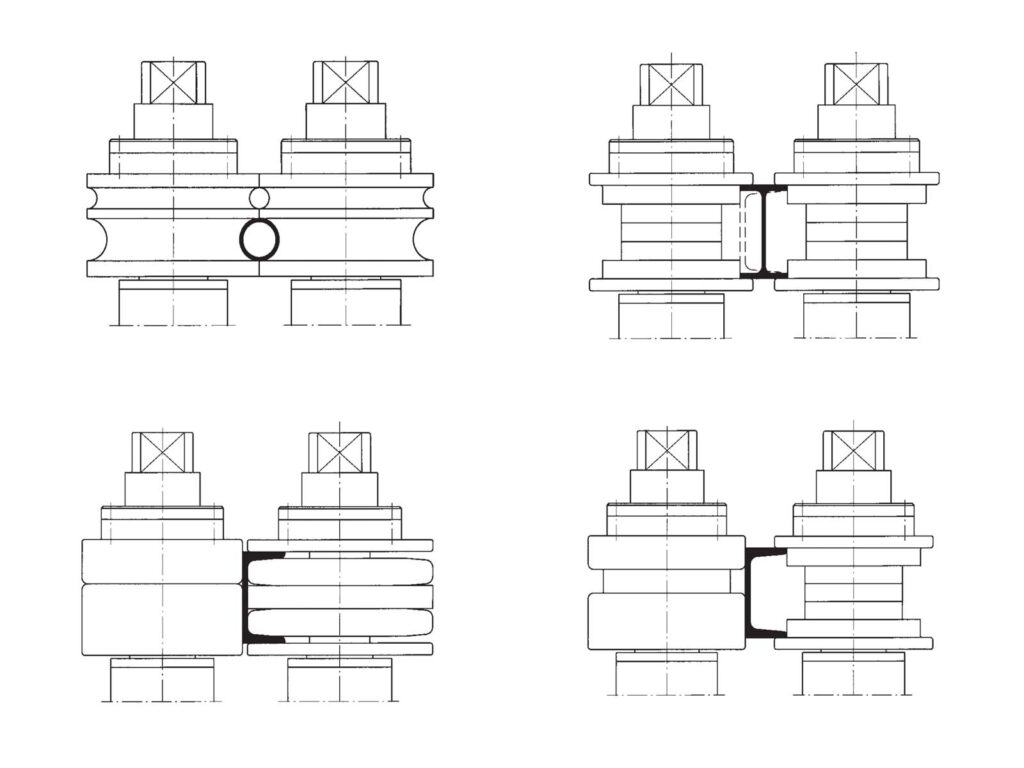
The PBC bending rolls are a set of universal rollers capable of processing all profile types (except circular/arc structural sections) through adjustable configurations.
Prior to profile bending (roll bending), the three-roll system must be precisely set up according to the specific cross-section being processed (angle iron/channel/T-bar, etc.). Proper roller alignment is critical to prevent equipment overload and profile deformation.
Profiles with arc transitions require matching radiused rollers
Section rolling: Roller groove width should match the profile thickness exactly, profile should pass through under slight compression.
Edge bending of flat bars: Upper roller groove width = material thickness + (2-4)mm, selection based on material thickness grading.
Pre-Clamping / Pre-Bending
Before profile rolling begins, operators use pre-clamping or pre-bending to shape the profile for smoother forming. This involves slightly curving the profile’s edge before it enters the profile bending machine. By securing the tail end in advance, operators prevent edge wrinkles or surface defects and ensure a seamless transition between straight and curved sections. This preparation improves bending precision, enhances control, and reduces material strain, minimizing the risk of deformation.
Pre-Bending Steps for Achieving a Smaller Unbent End Flat
Position the material between the rolls with the lower rolls aligned tangentially (see Fig. 1).
Move the profile slightly backward (see Fig. 2).
Slightly raise the right lower roll (see Fig. 3).
Feed the material forward by about 50–80 cm (see Fig. 4).
Use reverse rotation to move the material backward (see Fig. 5).
Raise the right lower roll again (see Fig. 6).
Repeat the pre-bending step; the curve will now be more pronounced (see Fig. 7).
If needed, repeat the process once or twice more until the desired diameter is achieved.
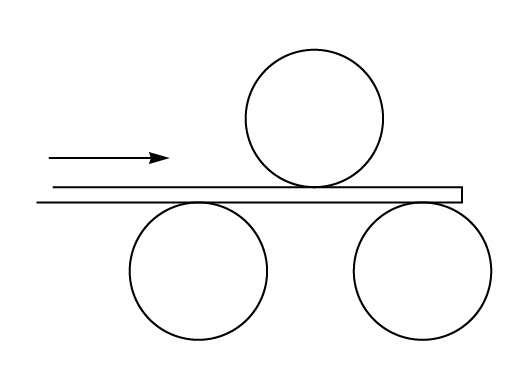
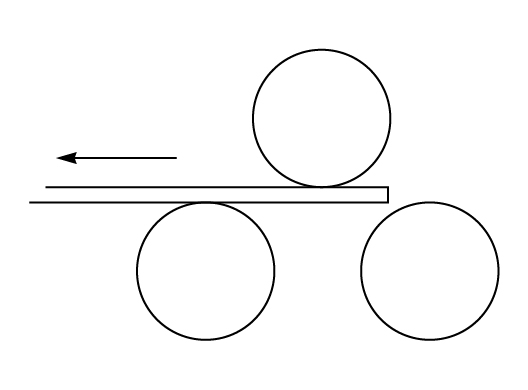
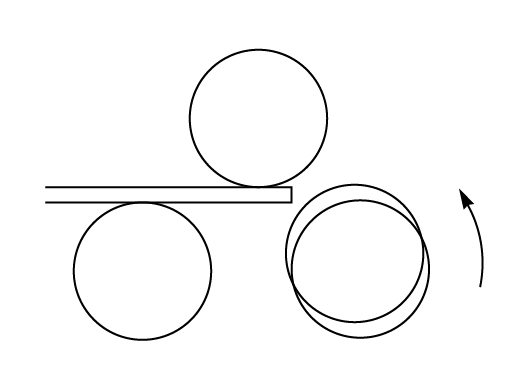
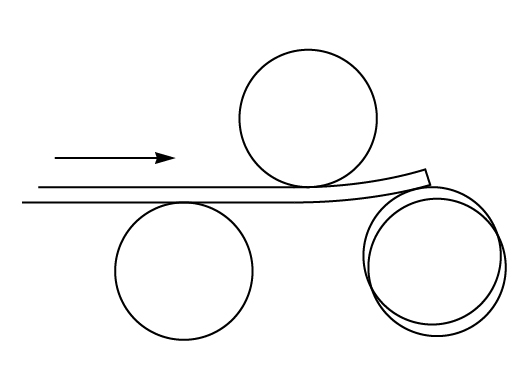
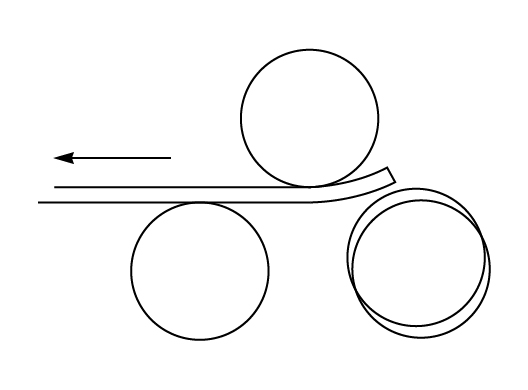
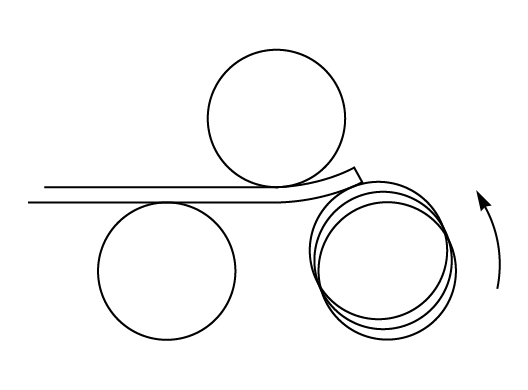
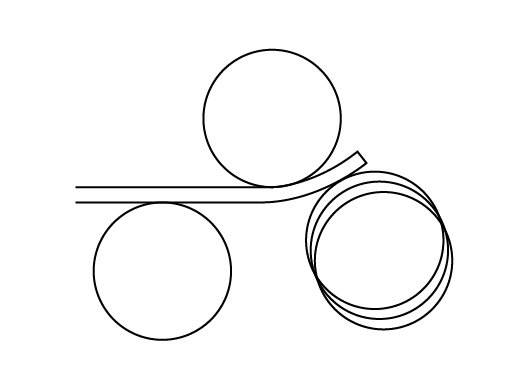
Profile Rolling
After setting the bending parameters, the metal profile is securely positioned, and pre-clamping or pre-bending is completed. Once the machine is started, the profile passes through the rollers, where controlled pressure is applied, gradually bending it to the desired curvature. During the process, real-time adjustments can be made to ensure precise specifications are met. The rollers apply uniform pressure along the entire length of the profile, achieving smooth and consistent forming results while maintaining material integrity. Each pass through the bending machine results in continuous deformation of the profile.
The accuracy and continuity of the radius primarily depend on the uniformity and homogeneity of the workpiece. Since material consistency is often difficult to achieve, the bent piece typically requires multiple passes through the roller bending process to achieve the desired radius accuracy.
The PB series is equipped with an intelligent CNC system, which automatically performs tasks previously carried out by experienced operators (including real-time measurement and automatic adjustment of the bending radius), significantly reducing labor and training costs.
Full Circle Section Rolling Guide

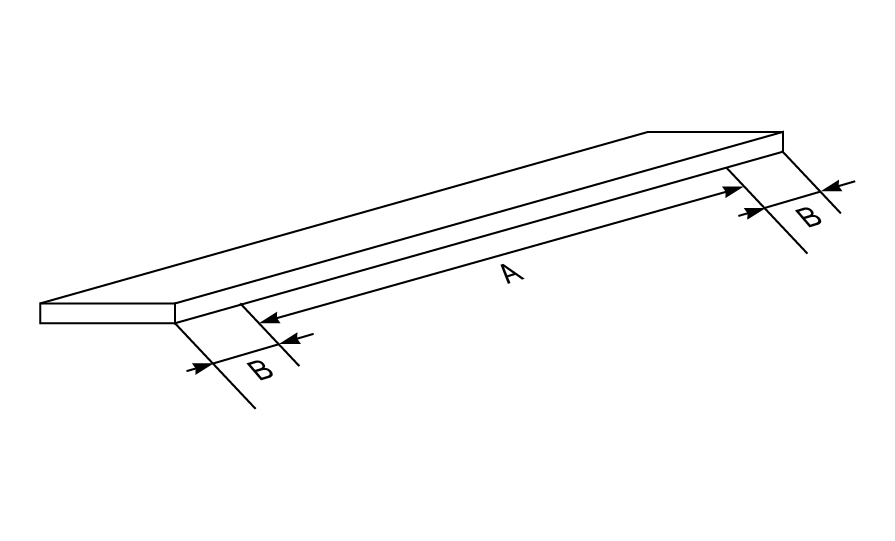
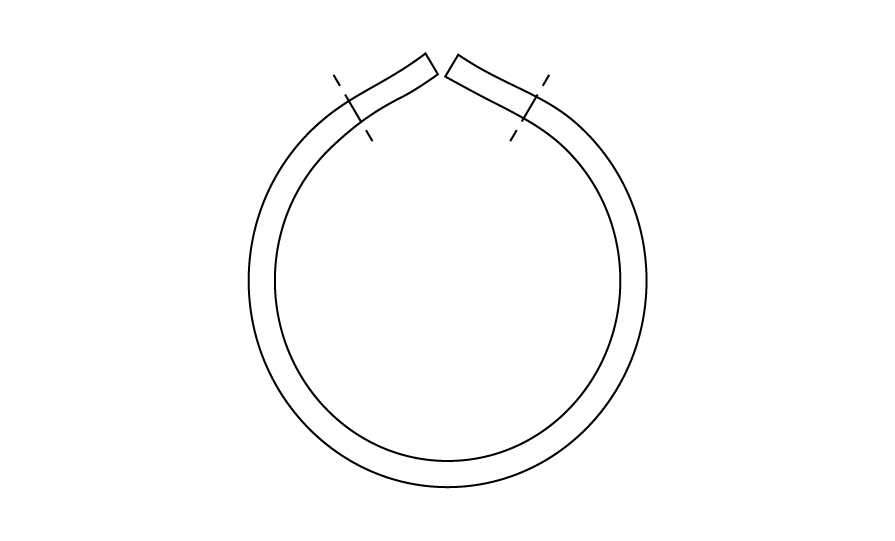
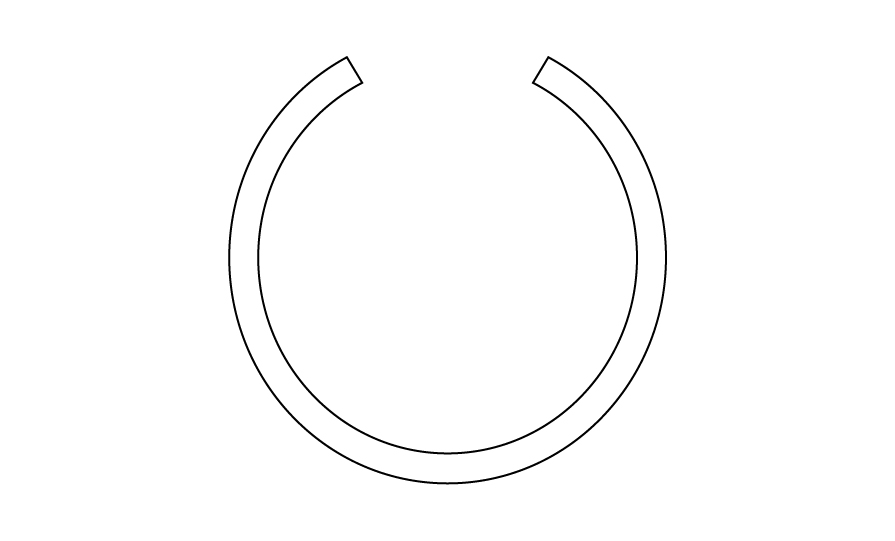
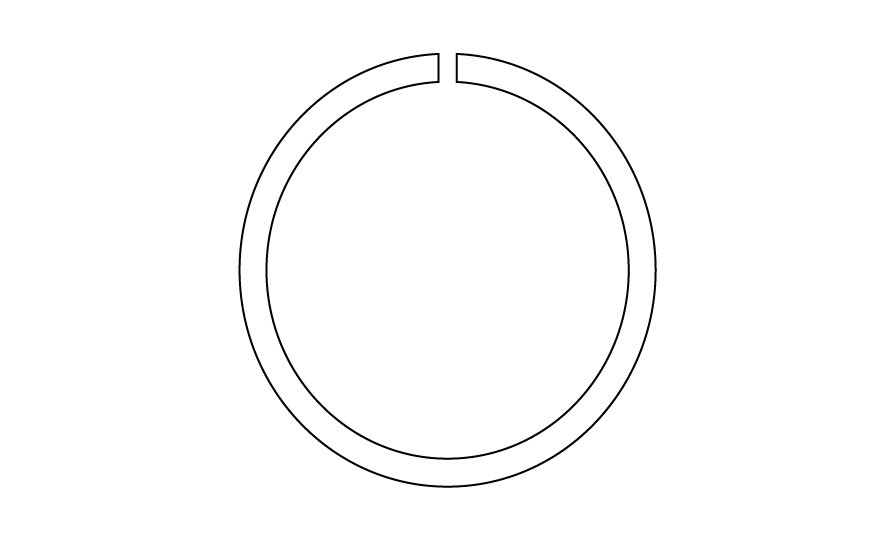
How to Accurately Achieve a Closed Circular Ring (as shown in Fig. 1)
To ensure a fully closed ring with a precise circular shape, follow these steps: Allow Extra Length: Cut the profile 10–20 cm longer than the required final length (Fig. 2)
Initial Bending: Bend the profile until the ends nearly meet (Fig. 3)
Trim the Ends: Cut off the unbent sections at both ends (Fig. 4)
Final Closure: Pass the ring through the rolls again until the ends are fully joined (Fig. 5).
This method results in a highly accurate, near-perfect circular ring.